混合集成(Hybrid Integration),指的是在将多种不同功能的光学器件集成在单一系统中,以实现紧凑、高效的光学系统。光学集成广泛应用于光通信、光子计算、传感、激光器和其他光电系统中。其目标是通过缩小体积、减少功耗和提高性能,实现更高密度的光子器件和更复杂的功能。相比起传统的单片集成,混合集成的制造过程简单,成本较低,并且功能性不被单一平台限制。不同的芯片之间可以通过光纤或者自由空间光学器件进行连接,大大增加了系统的复杂度和多用性。
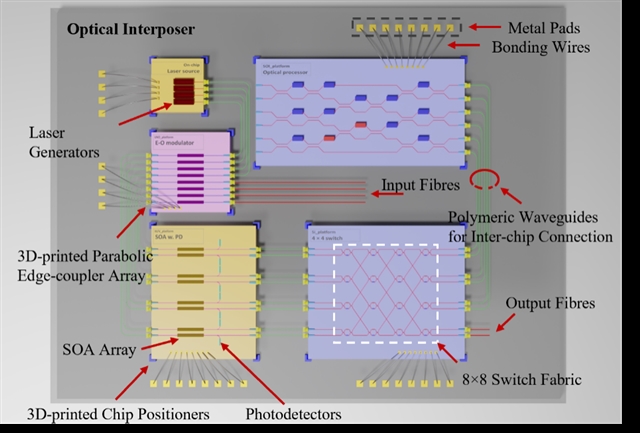
图1:通过3D打印集成的芯片组示意图
但是由于不同光学材料平台的折射率,边缘光学模场大小的不同,混合集成面临着耦合效率低,器件对准难,材料兼容性差,加工工艺复杂以及可靠性差等问题,阻止了其被进一步地大范围使用。
针对这些局限性,剑桥大学程祺翔团队通过利用亚微米量级精确度的3D打印技术,在芯片边缘以及基底上设计和制造了机械稳定结构和光学耦合结构,提出了一种新的光学跨平台互联体系。
该成果以“Photonic Chiplet Interconnection via 3D-Nanoprinted Interposer”为题发表在Light: Advanced Manufacturing.
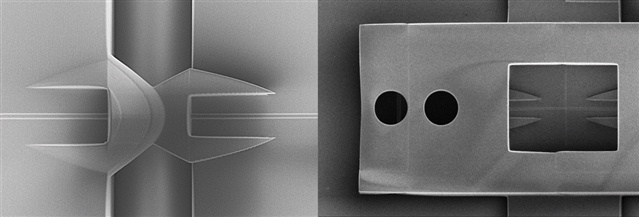
图2: 光学设计以及光纤插入隧道设计
1. 光学设计
在本研究中,研究者们通过使用一对3D打印的具有抛物面表面的反射镜,将光纤的输入光源经过两次全内反射后,被集成光芯片上的波导接收。通过调整抛物面的几何尺寸,输出光的模场大小可以被精确调控,从而可以实现任意平台之间的光学模场匹配。
2. 力学设计
除光学设计之外,研究者们还进行了配套机械结构的设计,从而可以实现光学芯片之间的预对准以及光纤和芯片之间的辅助对准。机械结构包括3D打印的光纤插入隧道以及基底上的芯片固定装置。通过精确的设计以及制造,机械结构可以有效降低对准难度,以及增强打印设备的稳定性。
在设计完成后,研究者们根据设计结果进行了一系列的加工及以测试:
1. 光纤到芯片的耦合测试
通过在芯片的波导两端打印光学以及机械辅助对准结构,以及在使用光学平台 插入裸光纤之后,实验测试证明在1550nm附近的宽波段下,该器件可以实现每个表面2.4dB左右的光学损耗。
2. 光学芯片组互联
在完成光纤-芯片耦合测试后,研究者们进行了进行了磷化铟和硅芯片之间的互联测试。测试中使用的芯片都来源于商业化的多项目晶圆芯片。对于芯片之间不同的模场大小,研究者们对模型的抛物面反射镜几何尺寸,光纤插入隧道孔径大小以及基底上芯片固定装置的位置进行了优化。经测试,硅芯片和磷化铟芯片之间的耦合损耗大约在2.5dB。并且通过更进一步的打印设定和几何尺寸优化,芯片之间的光学损耗可以被降低到1dB以下。
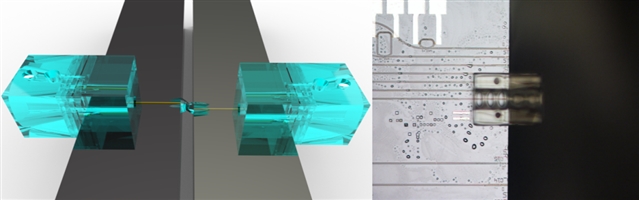
图3: 硅芯片和磷化铟芯片互联示意图以及打印器件件的光学显微镜图
相比起先前的研究,该研究的优点体现在:
1. 不需要任何的芯片后处理,可以直接在商业的多项目晶圆上直接制造光学结构。通过内嵌的对准镜头,可以实现亚微米级别的对准。
2. 设计的光学结构可以实现5:2的模式输入输出大小比,这也是目前文献记载的基于3D打印技术耦合器的最大模式大小比。
3. 设计了具有普适性的光学以及机械结构,对于不同的芯片,只需要微调设计的几何参数,无需重新设计。
4. 通过光学和机械结构的协同工作,可以大大降低对准难度,增大器件的对准容差。
5. 相比起传统的光学制造工艺,该制造过程耗时短,价格低,稳定性强,具有广泛的材料兼容性。
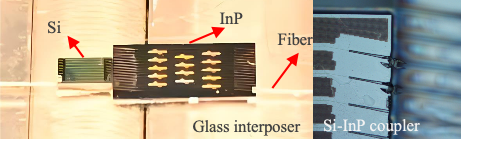
图4: 硅芯片和磷化铟芯片互联以及打印在芯片边缘的光学耦合器显微镜图
综上所述,研究者们基于亚微米精度的3D打印技术,设计了一套光学和机械的互联体系,实现了不同光学材料平台间的混合集成。
此项技术的应用不限于特定的两个光学平台之间,它也可以在多种不同的光学平台之间进行互联。这项技术打破了光学混合集成的瓶颈,无需复杂昂贵的制造技术和较长的制造时间,可以将不同的材料平台快速,方便,准确地集成为一个系统,在光学传感,光计算,光通讯等领域地应用前景十分广阔。(来源:先进制造微信公众号)
相关论文信息:https://doi.org/10.37188/lam.2024.046
特别声明:本文转载仅仅是出于传播信息的需要,并不意味着代表本网站观点或证实其内容的真实性;如其他媒体、网站或个人从本网站转载使用,须保留本网站注明的“来源”,并自负版权等法律责任;作者如果不希望被转载或者联系转载稿费等事宜,请与我们接洽。