|
|
FSCE | 前沿研究:中国特大跨径桥梁技术回顾与展望 |
|
论文标题:Design and construction of super-long span bridges in China: Review and future perspectives(中国特大跨径桥梁技术回顾与展望)
期刊:Frontiers of Structural and Civil Engineering
作者:Wei HUANG, Minshan PEI, Xiaodong LIU, Ya WEI
发表时间: 21 Jul 2020
DOI:10.1007/s11709-020-0644-1
微信链接:点击此处阅读微信文章
摘要/Abstract
本文概述了近三十年来中国特大跨径桥梁建设的基本情况,介绍了中国特大跨径桥梁上部结构、下部结构、钢桥面铺装的典型结构型式和设计、施工关键技术以及一些结构的运营使用状况,总结了中国特大跨径桥梁在安全、耐久、减灾防灾方面的技术现状,回顾了中国特大跨径桥梁在标准体系、高性能材料、信息化技术、工程装备以及监测评估等方面取得的进步,并对未来特大跨径桥梁技术发展方向进行了展望,以期为未来特大跨径桥梁的建设发展提供参考,助力中国快速迈入桥梁建设强国的行列。
关键词/Keywords
特大跨径桥梁 设计 施工 技术 进步 展望
0 引言
桥梁是交通基础设施的重要组成部分,为国家经济社会的发展提供重要支持。中国自古以来就是桥梁建设大国,特别是近三十年来保持着年均增长3万座桥梁的建设速度,极大地推动了中国交通行业的发展。特大跨径桥梁设计要求高、施工难度大,是衡量一个国家桥梁技术水平的重要指标。中国特大跨径桥梁设计相对起步较晚,直到上世纪九十年代,随着中国经济发展的迫切需求,中国各类跨江、跨山与跨海特大桥梁才相继建设。1991年建成的上海南浦大桥主跨达423m,开创了中国修建400m以上大跨径斜拉桥的先河。1993年建成的上海杨浦大桥跨径超过600m,成为当时世界上跨径最大的斜拉桥。与此同时,中国首座现代悬索桥——汕头海湾大桥(主跨452m)与首座跨径超千米(1385m)的钢箱梁悬索桥——江阴长江大桥也相继建成通车。此后,中国特大跨径桥梁的建设开始呈井喷式的发展趋势,因此,对特大跨径桥梁的设计技术的要求也随之提出。
进入21世纪,中国已经成为世界特大跨径桥梁建设的中心舞台。据不完全统计,世界上已建成400m以上跨度的斜拉桥中中国占比超过59%(其中3座在中国香港);世界上已建成500m以上跨度的悬索桥中中国占比超过39%(其中1座在中国香港);世界上已建成300m以上跨度的拱桥中中国占比超过55%。表1~表4分别列出了目前排名世界前十跨度的斜拉桥、悬索桥、拱桥和跨海大桥。在经历了追踪学习国外建设经验的阶段后,中国逐渐发展了具有自主创新产权的大跨径桥梁设计、建设与维养技术,极大地推动了中国乃至世界桥梁工程的发展。
表1 世界排名前10的斜拉桥
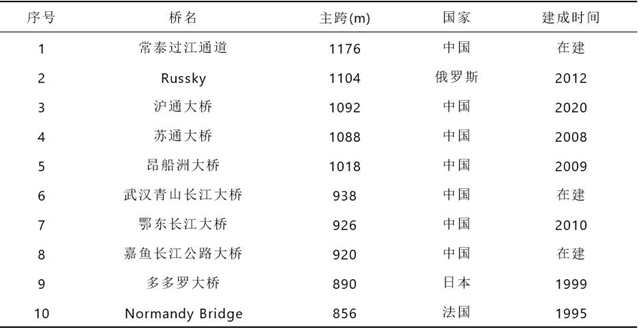
表2 世界排名前10的悬索桥
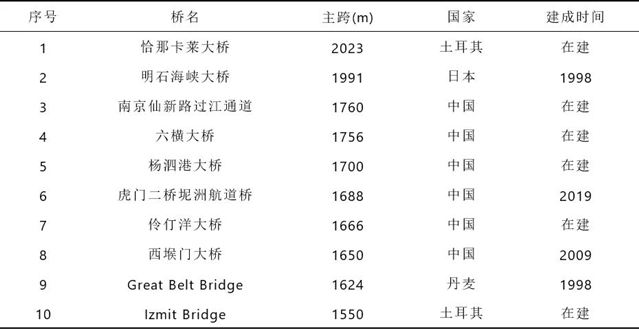
表3 世界排名前10的拱桥
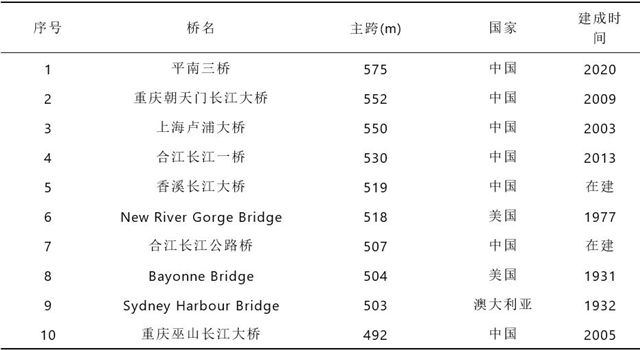
表4 中国世界排名前10的跨海大桥
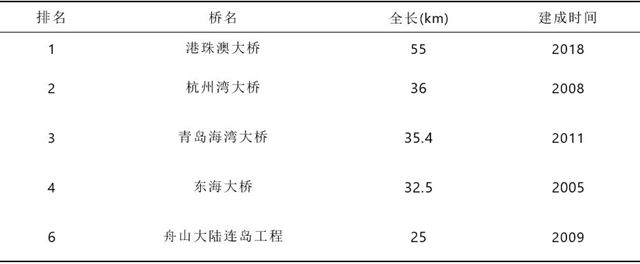
大跨径桥梁的建设不仅有助于推动交通行业的发展,也是一个国家科技实力的重要体现。本文总结过去三十年里中国特大跨径桥梁在上部结构、下部结构与桥面铺装等方面的设计、施工关键技术,介绍一些结构目前的运营使用状况,提出并展望未来特大跨径桥梁技术发展及应用趋势,以期为未来特大跨径桥梁的建设发展参考,助力中国快速迈入桥梁建设强国的行列。
1 中国特大跨径桥梁建设的基本情况
斜拉桥、悬索桥与拱桥是特大跨径桥梁常见的结构形式,在中国特大跨径桥梁建设中都有着大量的应用,三十年来不断取得进步与发展。
1.1 特大跨径斜拉桥
斜拉桥主要由索塔、主梁、斜拉索组成。目前中国已建成的斜拉桥超过100座,根据斜拉桥主梁结构形式的不同,选取了苏通长江大桥、沪通长江大桥和鄂东长江大桥三个典型的斜拉桥介绍如下。
苏通长江大桥[1]于2008年建成通车,主跨达1088m,是当时世界最大(目前为第三)跨径斜拉桥,采用双塔双索面钢箱梁及七跨连续结构体系。其300.4m高的桥塔与577m长的拉索曾是世界之最,在施工中通过技术革新成功解决了包括主体结构、抗风、抗震、防撞、超大群桩基础施工、超高钢混桥塔设计等10多项技术难题,先后获得2008年“乔治•理查德森奖”、2010年美国土木工程师协会杰出工程成就等国际大奖。
沪通长江大桥[2]主航道桥是世界上首座跨度超过1000米的公铁两用斜拉桥,采用主跨1092米的双塔三索面钢桁梁斜拉桥结构。主塔高325米,采用倒“Y”形,主塔基础采用倒圆角的矩形沉井基础方案,平面面积达5100m2, 是世界上规模最大的桥梁沉井。主梁使用新研发的Q500qE高强桥梁钢;世界上首次采用伸缩量2000毫米级的桥梁轨道温度调节器和伸缩装置。
鄂东长江大桥[3]主跨926米,是世界上已建成的第二大混合梁斜拉桥,中跨主梁采用钢箱梁,边跨采用同外形的混凝土箱梁;钢-混凝土结合段长8.5米,且位于中跨桥塔附近,结合段采用PBL剪力连接器的多格室传力构造,实现钢梁向混凝土梁传力的过渡。该桥也采用全寿命设计理念, 进行钢筋混凝土耐久性及钢结构防腐设计,设置桥梁各主要构件检查维护通道。
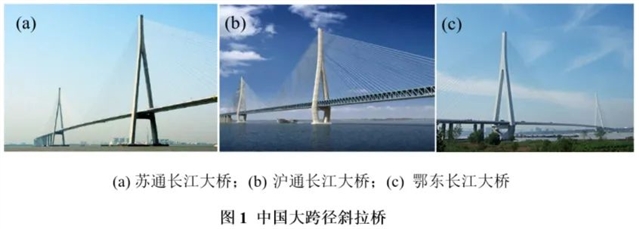
1.2 特大跨径悬索桥
悬索桥主要由主缆、桥塔、吊索、锚碇与加劲梁等组成,是当前跨度超过1000米桥梁的主要桥型。上世纪90年代中期,广东汕头海湾大桥开启了中国现代大跨径悬索桥的建设,之后中国悬索桥的跨越能力不断得到提升,1999年建成的江阴长江大桥是中国第一座主跨长度超过1000m的悬索桥。
舟山大陆连岛工程西堠门大桥[4]是世界首座分体式钢箱梁悬索桥,采用两跨连续结构,跨径布置为578m + 1650m + 485m,是世界上跨度第二、钢箱梁长度最长的在运营悬索桥。采用的分体式钢箱加劲梁方案,显著提高结构颤振稳定性能,可抵抗17级超强台风,建设期间成功经受两次台风的考验,开创中国强台风区特大跨径钢箱梁悬索桥的实践先例,获得了菲迪克2015年度“杰出工程项目奖”。
海沧大桥[5]为三跨连续全漂浮钢箱梁悬索桥,跨径布置为230m+648m+230m,是中国首座系统地进行桥梁景观设计的特大型桥梁,以曲线造型为基调,从多方面保证大桥与自然环境的融合。
泰州长江大桥[6]是世界上首座三塔双跨钢箱梁悬索桥,主跨2×1080m,与传统的两塔悬索桥相比,三塔两跨悬索桥通过增设中间塔的方式,实现结构的连续性布置,通过中塔的变形来承担活载造成的两边主缆的受力差异。此外,泰州大桥也创下了当时的4项世界第一:索塔采用纵桥向倒“Y”形、横向门式框架型钢塔;由于河床断面呈W形且河段土质松软,中间塔基础入土深度达70m,为世界第一;世界上首先采用W形主缆,架设长度3117m;施工中史无前例采用两跨钢箱梁同步对称吊装。2014年,泰州大桥被国际桥协授予“2014年杰出结构工程奖”。
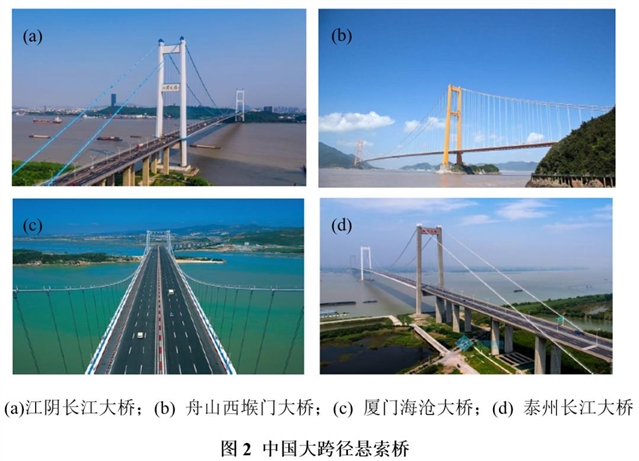
1.3 特大跨径拱桥
拱桥在中国的发展历史超过一千多年,中国现代大跨径拱桥以跨江与跨山谷大桥为主, 多次设计建成不同时期不同形式世界最大跨度拱桥,我国拱桥的建设技术已处于世界领先水平。
上海卢浦大桥[7]主跨550m,保持了6年世界最大跨度拱桥的记录,大桥为钢箱拱桥,首次完全采用焊接工艺连接。大桥建造中的焊缝总长度、肋拱吊装重量、用钢量、系杆索长度及张拉吨位等均是当时的世界之最, 获得了国际桥协2008年“杰出结构工程奖”。
重庆朝天门长江大桥[8]是世界上已建成跨度最大的桁架拱桥,设计为190m + 552m + 190m三跨连续中承式钢桁系杆拱桥,双层桥面,上层设双向6车道及两侧人行道,下层布置双向城市轨道。全桥布置两层系杆,上层采用“H形”截面钢系杆,下层采用“王形”截面钢结构+体外预应力索系杆。大桥建设克服了严重破碎漏水岩层基础施工、552m跨钢桁拱悬臂拼装、高温、高湿地区高强螺栓施工控制、钢桁拱及刚性系杆合龙精度控制等8项难题。
南京大胜关长江大桥[9]是京沪高铁的控制性工程,可满足时速300km/h的高铁运行要求,创造了“体量大、跨度大、荷载大、速度高”四项世界第一。大桥全长9.27km,主桥为6跨连续钢桁架拱桥,主跨2×336m,该连拱为世界同类级别最大跨度,大桥获得国际桥协2015年“杰出结构工程奖”。
沪昆高铁北盘江特大桥[10]是世界上跨度最大的钢筋混凝土拱桥,可满足时速350km/h高铁运行,大桥全长721m,主跨445一跨跨过北盘江。大桥突破了大跨度桥梁无砟轨道铺设、大跨度混凝土拱桥施工与刚度控制等难题,使用的C80混凝土钢管拱结构为中国首创,大桥获得了国际桥协2018年“古斯塔夫•林德撒尔奖”。
2020年12月建成通车的平南三桥,再次刷新世界最大跨径拱桥纪录。大桥位于广西壮族自治区贵港市平南县,设计为主跨575米的中承式钢管混凝土拱桥,首次在拱桥中采用“圆形地连墙+卵石层注浆加固”的拱座基础方案,应用北斗卫星定位系统、智能张拉等技术,将200米高度的塔架顶部偏位精确控制在20毫米以内;首创基于影响矩阵原理的“过程最优,结果可控”扣索一次张拉计算理论,实现大跨径拱桥主拱圈线形控制技术的新突破,使9000吨拱肋合龙精度在3毫米内;首创采用C70自密实无收缩复合膨胀混凝土,运用真空辅助连续四级泵送工艺,助力钢管混凝土拱桥管内混凝土灌注施工品质迈上新的台阶。
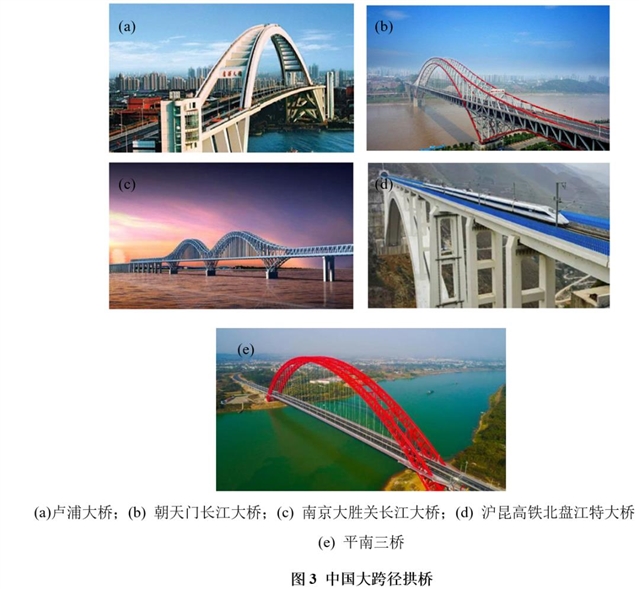
2 中国特大跨径桥梁的设计技术
2.1 全寿命设计理论
大跨径桥梁兴建初期,世界各国的桥梁设计往往仅重视建设技术和结构安全,没有涉及桥梁使用期的管理、养护、维修、构件更新、拆除等诸多问题,只注重建设期的投资成本而不重视桥梁整个寿命周期内的总成本[11]。第二代桥梁设计理论采用可靠度理论评估桥梁使用寿命,实现结构耐久性设计,但仍然存在生态友好欠佳、材料构件不能满足寿命周期耐久性要求等问题。为改善大桥的运营质量,美国、日本和芬兰等国首先开始重视大跨径桥梁的全寿命周期设计,主要考虑全寿命周期费用、生态友好性、结构安全性等[11]。当前中国桥梁设计方法已发展为基于全寿命周期费用、绿色交通和结构性能化的第三代工程使用寿命设计理念[11]。桥梁全寿命设计理念是桥梁发展的必然趋势,中国学者在基于构造细节的全寿命设计方法[12]、全寿命周期内的养护管理以及风险评估[13-14]、全寿命周期成本计算以及全寿命理念的桥梁管理[15-16]等方面开展了研究,并不断涌现出新成果。
2.2 上部结构设计
大跨径桥梁上部结构一般包括:钢梁(钢箱梁或钢桁梁)、索塔或拱、缆索系统、桥面铺装及附属设施等,现以钢箱梁及索塔为代表予以介绍。
2.2.1 钢箱梁设计
钢箱梁是大跨径桥梁主梁常用的结构形式,常分为若干节段,通过预制吊装完成。其于1958年由Geoge Stephenson提出并首次应用。中国于上世纪90年代起开始兴建大跨径钢箱梁桥,得到了越来越广泛地应用。
2.2.1.1 钢箱梁总体设计
钢箱梁的截面形式多为整体单箱,少量采用分离双箱形式,参见图4,采用整体单箱截面形式如苏通长江大桥、江阴长江大桥等[17-18],采用分离双箱断面形式如舟山西堠门大桥[19]。
钢箱梁是由顶板、腹板及底板等构件通过焊接形成的一个闭合的流线型薄壁箱体结构,为增加箱体整体性及刚度,在箱体内沿桥纵向一定间距设置横隔板,有的桥也设置纵隔板。顶板、腹板和底板均为正交异性板结构,纵、横隔板上一般都设有加劲肋。通常,钢箱梁通过较大的扁平度、两侧的导风尖角来实现其抗风功能,必要时增设抗风导流板。中国部分大跨径桥梁的钢箱梁设计参数见表5。
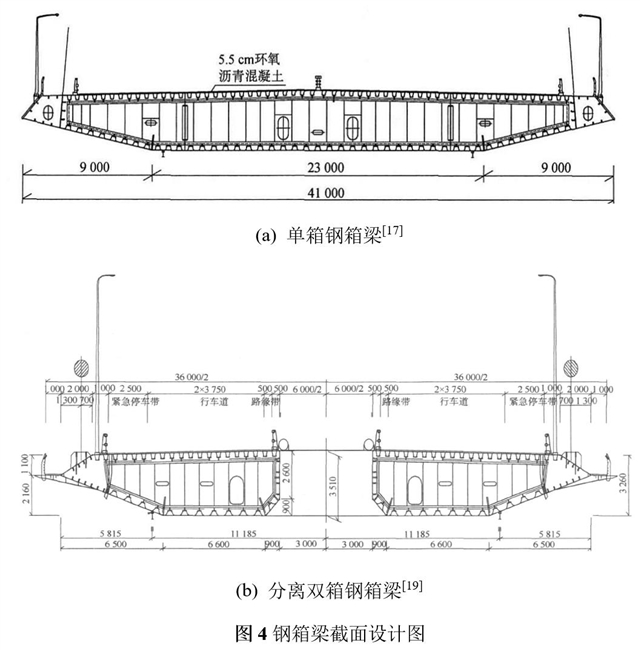
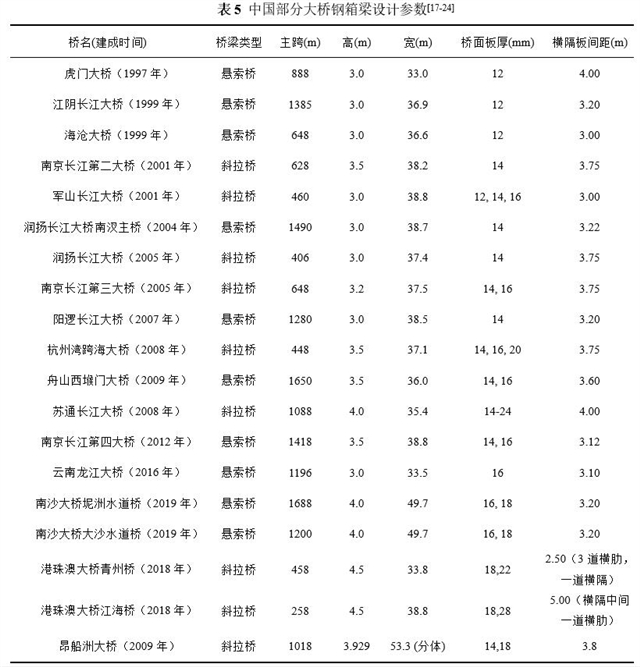
2.2.1.2 正交异性钢桥面板设计
正交异性钢桥面板由顶板及纵(横)向加劲肋等构件组成,其中纵、横向加劲肋垂直设置,与上部顶板共同承重。纵向加劲肋排列通常较为紧密,而横向加劲肋布置间距较大,这种特殊的结构形式使得钢桥面板在横纵方向上刚度不同,受力性能也呈现正交异性特征。正交异性板既可以作为梁体顶部结构参与箱梁的整体受力,又可以作为桥面板承受车辆荷载作用。正交异性钢桥面板上方铺设有一定厚度的铺装层,既提供车辆行驶,又起到将车辆荷载扩散至顶板作用。
正交异性板顶板厚度设计时常常以挠度控制为目标,中国《公路钢结构桥梁设计规范 》(JTG D64-2015)规定行车道处顶板厚度不小于14 mm,裸板横桥向的局部挠跨比应不大于1/700,含铺装的正交异性板横桥向的局部挠跨比应不大于1/1000。中国大跨径钢桥的顶板厚度一般在12~20 mm之间,初期顶板厚度常用12 mm,从使用状况看,顶板疲劳及桥面铺装寿命小于设计预期,后来的设计都增加了顶板厚度。
纵向加劲肋分为开口肋和闭口肋两种形式,如图5所示。开口肋的截面形式有平钢板、圆头角钢、L型以及倒T型等,其主要特点为:易于加工与连接,但抗弯、抗扭刚度较小;闭口肋的截面形式有V型、Y型、U型以及半圆型等,对制作精度和焊接工艺要求高,但抗弯、抗扭刚度大。综合受力性能、施工便利等方面考虑,大多数公路桥钢桥面板设计采用U型加劲肋。
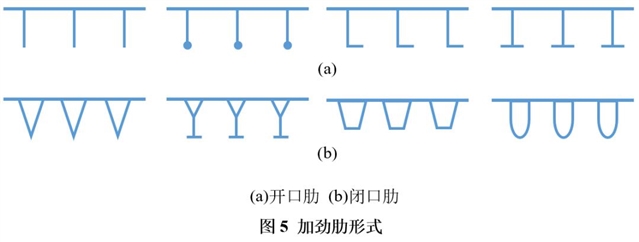
提高加劲肋的高度可提高抗弯惯性矩及刚度,但如果加劲肋高度过大,易发生局部屈曲。为减小应力集中,避免刚度变化过大并增强局部稳定性,中国《公路钢结构桥梁设计规范 》(JTG D64-2015)建议纵向加劲肋等间距布置,并连续通过横隔板或横向加劲肋。在厚度方面,各国规范规定U肋厚度均不小于6 mm。
中国一些钢桥U型加劲肋参数如表6所示,基本呈现标准化设计,上口宽300 mm或320mm,下口宽180 mm左右,高300 mm或280 mm,U肋中心间距600 mm左右。较早建成的大桥U肋厚度多为6 mm,在南京长江二桥建成后,中国大跨径钢桥的U肋厚度多为8 mm。
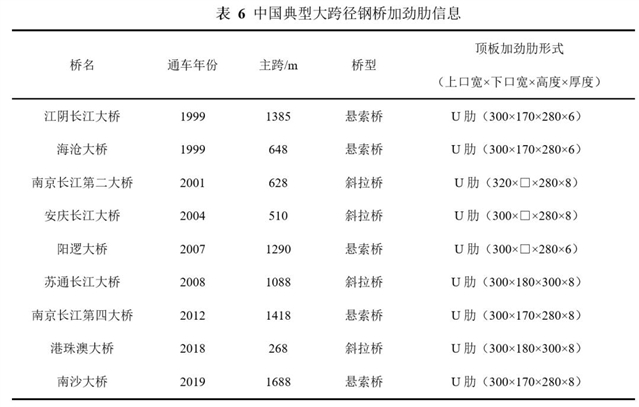
钢箱梁横隔板主要有肋式、桁架式和实腹板式三种,中国已建成的大跨径钢箱梁桥多采用实腹板式横隔板。《公路钢结构桥梁设计规范》 (JTG D64-2015)规定:采用闭口加劲肋的箱梁内横隔板间距不宜大于4 m,且在桥梁支点对应处必须设置横隔板,中国已建大跨钢箱梁桥横隔板间距一般为3.0~4.0 m,厚度一般为8mm~14 mm。
为降低纵向加劲肋穿越横隔板开口处的疲劳应力,各国规范均给出了推荐的开口形式,具体如表7所示。
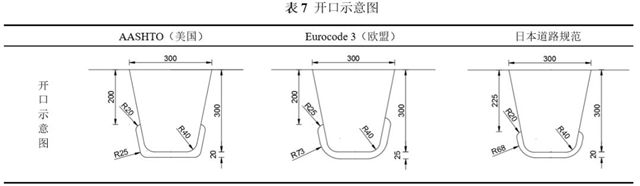
2.2.2 索塔设计
索塔是斜拉桥与悬索桥的重要组成部分,索塔的设计不仅要满足受力要求,还需获得好的美观效果。从横桥向看,常用的有单柱形、“A”字形与倒“Y”形索塔等;从纵桥向来看,常用的有柱式、“门”式、“A”字形以及倒“Y”字形等。柱式索塔通常用于主梁抗扭刚度较大的桥梁;对于抗风抗震要求较高的大跨径桥梁,常用横向刚度大的“门”式、“A”形与倒“Y”形的索塔形式[25]。
2.2.2.1 混凝土索塔设计及案例
混凝土索塔结构由塔柱与横梁组成,塔柱一般为钢筋混凝土薄壁空心截面,受力较大的横梁一般为薄壁箱型预应力结构,为提高塔柱局部及整体稳定性,在塔柱空心截面中沿高度方向按一定间距设置横隔板,并在塔底设置一段实心截面,实现与塔座的刚度匹配,星海湾大桥[26]采用了门式塔(图6a);苏通长江大桥[27-28]采用“A”字形混凝土索塔(图6b),塔柱采用空心箱型截面,根部塔柱为满足抵抗船舶撞击要求,下塔柱底部10m的范围内采用实心箱型截面;沪通长江大桥[29]桥面以上索塔采用倒“Y”形钢筋混凝土索塔(图6c),是结合其基础形式以及考虑抗风稳定性和经济性选取的,桥面以下塔柱内收为钻石形结构,桥塔高325m,塔柱及横梁全部采用C60高性能混凝土。
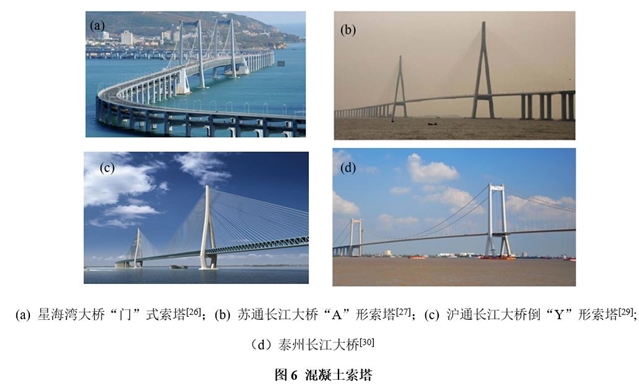
2.2.2.2 钢索塔设计及案例
相比混凝土索塔,钢结构索塔具有“自重轻、抗震性能好、易于造型、工厂化制造现场安装利于缩短工期、环保”等优点[31] ,但其要求更高的建造精度,中国建成的钢结构索塔以“人”字形与倒“Y”形较为常见。
南京长江三桥[32-33] 在国内首次采用“人”字形钢结构索塔,共设置有4道横梁,下塔柱与下横梁为钢筋混凝土结构,其余部分为钢结构,钢塔柱截面尺寸沿竖直方向保持一致;除钢混过渡节段外,每个钢索塔共分为21个节段,节段间连接方式为高强螺栓连接。钢索塔节段的精准安装成为建设的难点和重点,包括:钢索塔各节段空间位置的检测、轴线测量纠偏、顶面倾斜度检测以及塔柱空间尺寸的复核,采用“定位-调整-测量-定位”的流程逐步提高精度。
泰州长江大桥[30,34]为三塔两主跨悬索桥,若中塔刚度不足,则塔顶会产生较大的位移,桥面挠度将超出规范允许;若其刚度过大,会有主缆在塔顶产生滑移的风险。经研究,中塔设计为总体柔性,塔顶可允许发生一定的位移,但需控制在允许范围,为实现这个目标,中塔设计为纵桥向“人”字形的钢塔,调节尺寸配合,从而达到中塔的最佳刚度,中塔横桥向为“门”式结构,如图6d所示。两侧钢塔柱均分为21个吊装节段,包括首节段、下塔柱、合拢段、下横梁、上塔柱以及上横梁6部分, 各节段之间采用高强螺栓连接。
2.3 基础设计
2.3.1 锚碇基础
锚碇是悬索桥重要结构构件,主要形式包括重力式和隧道式,重力式锚碇以重力抵抗主缆拉力在竖直方向上的分力,以锚块与地基的摩擦力抵抗主缆在水平方向的拉力[35-36];隧道式锚碇以围岩自重、锚塞体自重抵抗主缆拉力在竖直方向上的分力,以围岩与锚塞体界间的楔形挤压力及界面上的抗剪断力抵抗主缆在水平方向的拉力,由于重力式锚碇在各种地质条件下均适用,所以目前应用最为广泛,如润扬长江大桥、南京长江第四大桥、江阴长江大桥、阳逻长江大桥及虎门大桥等。重力式锚碇基础根据地质条件不同,可采用板式或筏式扩大地基、沉井和地下连续墙。
润扬长江公路大桥[37]作为当时中国第一大悬索桥,锚碇基础以微风化基岩为持力层,采用矩形地下连续墙方案(图7a ),以地下连续墙与内衬组合的形式来构成基本的基坑结构,并通过浇筑、回填钢筋混凝土最终完成基础施工。
南京长江第四大桥南锚碇基础[38]采用“∞”形地下连续墙结构(图7b) ,该类结构形式的基础可以通过自身的形状优势利用“拱效应”来抵抗侧向土压力,具有较好的抑制结构变形的能力。基础以中风化砂岩为基底持力层。
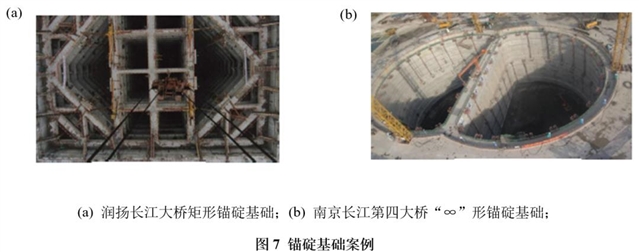
2.3.2 群桩基础
群桩基础是斜拉桥及悬索桥主塔基础最为常见的形式之一。群桩基础具有承载力大、沉降量小等优点, 经常被用做桥梁结构的基础形式,适用以下情况:荷载较大、地基上部土层软弱、适宜的持力层位置较深、采用刚性扩大基础困难大、其它方案在技术经济上不合理。该基础形式不需要大范围开挖,减少了支护、降水等工作。苏通长江大桥[17]主塔基础是世界上规模最大的群桩基础,基础构造如图8a。桩基由131根直径2.8m或2.5m的钻孔灌注桩组成,呈梅花形布置,桩长117m。承台为哑铃型,长113m,宽48m,厚度由边缘的5m增大到中间的13m。为了减轻船舶撞击与地震的影响,设计采用了永久钢护筒与钢筋混凝土桩共同承力的组合模式,这种组合形式提高了桩的承载力,也因无需拔出钢护筒而提高了工效。
2.3.3 沉井基础
沉井基础能承受较大的垂直荷载和水平荷载,对地基承载力的要求相对较低,更适用于深水地区。沉井具备多种功能,其可作为基础结构的同时,也可在施工时作为挡土和挡水的围堰结构物。若沉井基础在着床定位过程中存在偏差,可将该段沉井腔室内的水排出,当该段沉井基础上浮后,重新进行着床定位。
60年代中国在修建南京长江大桥时,发展了重型混凝土沉井、深水浮运钢筋混凝土沉井以及钢沉井,实现了沉井在中国深水桥梁基础中的应用。泰州长江公路大桥[39]中塔墩沉井基础是目前世界上入土深度最大的水中沉井基础,基础构造如图8b。基础采用圆角矩形沉井,断面尺寸为58m × 44m,总高度为76.0m。下部为钢壳混凝土沉井,分为7个节段。首节段在岸上预制,并在水中接高至38m,在壳体内浇筑混凝土使其下沉。上部38m为钢筋混凝土沉井,分为5个节段浇筑。沪通长江大桥[40]主塔也采用倒圆角矩形沉井基础,基础尺寸达到86.9 m×58.7 m×115 m,是当时世界上最大的沉井基础。钢沉井井壁采用双壁隔舱结构,可以在下沉中充分利用水的浮力,通过调节隔舱内的水位,来调节沉井位置。
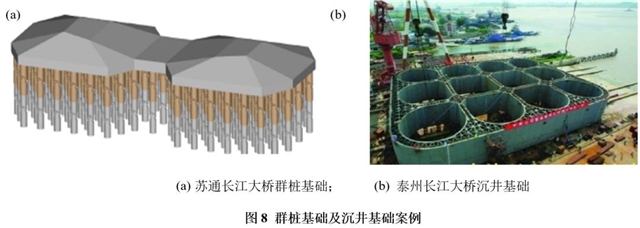
2.4 钢桥面铺装设计
大跨径钢箱梁桥面铺装层的主要功能是在设计期内为车辆提供安全、平整、稳定的行驶路面,要求铺装层具有较高的强度及耐久性,较好的耐磨性及抗滑性,优良的高温稳定性、低温抗裂性以及防水防渗透能力,还需要与顶板有较好的变形协调性能[41]。正交异性板不仅作为钢箱梁的顶板,也直接作为桥面沥青铺装层的底板。由于正交异性板结构刚度小,因此钢桥铺装层比普通高等级公路上沥青混合料面层受力更加复杂,在外力作用下容易受压、受剪破坏。在重型车辆反复碾压后,沥青混合料会因蠕变变形或永久变形而产生车辙,且铺装层与钢板的粘结性能在高温和荷载作用下很难满足工程要求,所以大跨径钢桥面铺装已经成为一个世界性的难题[42-43],是近二十多年来中国大跨径桥梁研究投入最多的领域之一,并取得了丰硕的成果,使得该项技术取得世界领先地位。
2.4.1 铺装材料类型
钢桥面铺装材料主要有环氧沥青混合料、浇注式沥青混合料及沥青玛蹄脂碎石(SMA)三种,设计研究内容主要集中在沥青混合料与集料级配两方面。针对钢桥所在自然环境与使用条件的特点,对沥青与集料进行选择并对集料级配进行调整优化[44-46]。
2.4.1.1 环氧沥青混合料
环氧沥青是通过将环氧树脂加入沥青中,与掺入沥青中的固化剂发生固化反应后形成的一种不可逆的固化物。这种材料从根本上改变了沥青的热熔性质,赋予了沥青优良的物理力学性质。环氧沥青混合料具有优异的力学特性及路用特性,在低温时韧性良好,高温时不熔化,同时具有密水性及抗裂性。
2001年建成通车的南京长江二桥是中国首次使用环氧沥青铺装的大跨径钢桥。由林同炎工程咨询公司作为技术顾问,东南大学团队进行了全面系统的研究,首先在中国成功地实现了超过十五年设计使用寿命的目标,第一、二车道运行20年至今未经大修仍保持较好的使用性能,是中国使用年限最长的大跨径钢桥面铺装[47-49]。之后,利用南京二桥的研究成果和成功经验,中国大跨径钢桥开始大批量使用环氧沥青作为钢桥面铺装,部分桥梁使用情况如表8所示。
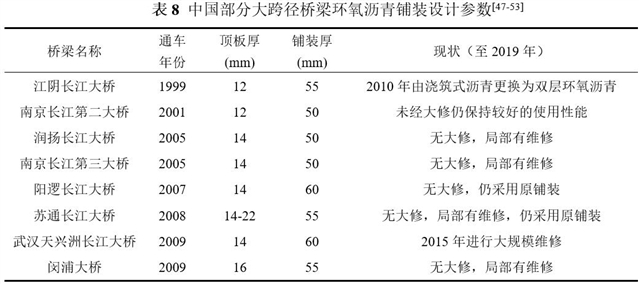
目前中国常用的环氧沥青包括美国ChemCo环氧沥青混合料、国产新型环氧沥青与日本KD-BEP环氧沥青混合料三种。
美国环氧沥青由两部分组成:环氧树脂和由石油沥青、固化剂及其它助剂组成的均质混合物;而日本环氧沥青由三部分组成:基质沥青、环氧树脂(主剂)和固化剂(硬化剂) [54]。由于美国环氧沥青的施工条件要求比日本环氧沥青苛刻,近些年中国大跨径钢桥的新建与养护多采用日本环氧沥青。自2005年以来,日本环氧沥青已在中国约15座桥梁中应用,抗高温稳定性及抗疲劳耐久性能良好。
中国对环氧沥青配置方法及机理的研究始于上世纪90年代,东南大学团队的研究成果斐然[55]。有百余位博士研究生先后开展相关研究工作,提出了大跨径桥梁钢桥面铺装的设计理论与方法[41,50,56],建立了基于疲劳等效的钢桥面铺装体系轴载换算方法[46],进行铺装结构的动力分析[57-58],并在三十多座特大跨径桥梁上成功应用[47-48,50]。研究团队还发明了国产新型环氧沥青及相关设备,打破了国外产品的高价垄断。相关研究表明,国产环氧沥青混合料具有良好的低温施工性能及宽泛的容留时间范围, 且其强度的发展主要取决于养生的时间及温度[59]。与SMA-10相比,国产环氧沥青混合料具有良好的高温稳定、抗疲劳、抗水损害及低温抗开裂性能[60]。与美国环氧沥青相比,国产环氧沥青混合料的早期强度与之相当,而后期强度增长期更长,强度更高。就综合性价比而言,中国环氧沥青是一种优良的大跨径钢桥面铺装材料。国产环氧沥青混合料60℃车辙试验几乎无变形,与美国环氧沥青具有相同优良的耐高温性能;同时,国产环氧沥青混合料低温劈裂残留强度比约为80%,比美国环氧沥青混合料高,且具有较好的水稳定性及耐油腐蚀性。国产环氧沥青已在武汉天兴洲长江大桥与上海长江大桥等数十座大桥成功应用。
2.4.1.2 浇注式沥青混合料
浇注式铺装材料起源于德国,并在欧洲及日本得到广泛应用。浇注式沥青混合料可以在190℃~240℃高温下,无需碾压、依靠自身流动性即可摊铺成型,且保证较低的孔隙率。德国一般称浇注式沥青混合料为guss asphalt,日本称其为高温拌和式摊铺沥青混合料,英法及地中海沿岸国家称其为沥青玛蹄脂。中国通常翻译为嵌压(碾压)式或浇注式沥青混合料。1999年江阴长江大桥借鉴英国技术,在国内首次采用浇注式沥青混合料铺装。但由于对高温稳定性与抗车辙性能要求考虑不足,加之超载车辆通行较多,大桥通车后不久即发生大面积破坏。2000年中国引进德国浇注式沥青混合料铺装技术及配套设备,2003年在山东胜利黄河公路大桥中得到应用,之后在多项桥面铺装等特殊铺装工程中推广[61]。随着我国钢桥面铺装技术的持续提高,浇注式沥青混合料的性能得到了很大改善。由于其独特的防水、抗老化、抗疲劳性能以及对钢桥面板优良的追从性和粘结性能,适用于作为下层铺装结构。目前,浇注式沥青混合料在国内钢桥面铺装领域所占的比重接近50%[62],并且形成了多种铺装方案,如浇注式沥青混合料+改性沥青 SMA、浇注式沥青混合料+环氧沥青混凝土、浇注式沥青混合料+开级配抗滑磨耗层OGFC。
与传统沥青混凝土及沥青玛蹄脂碎石 SMA 的成型方式不同,浇注式沥青混合料成型时既不需要击实,也无需旋转压实,只需经过短时间的振动即可使混合料达到设计要求。浇注式沥青混合料的这种特点使传统的马歇尔设计法及体积设计法均不能适用[63]。根据日本、德国研究浇注式沥青混合料的工程实践,浇注式沥青混合料的设计采用刘埃尔流动度(Lueer Test) 、贯入量(Indentation Test)、动稳定度、低温极限弯曲应变等作为控制指标[64-65]。
2.4.2 铺装结构设计
中国大跨径钢桥面铺装设计的相关研究始于上世纪八十年代,但这些研究成果应用于上世纪的大跨径钢箱梁桥上鲜少取得成功。一般情况下,2-3年后桥面铺装均发生了大规模病害而不得不进行大修或重新铺装。
东南大学团队经系统研究,发明了薄层铺装结构,解决了开裂、脱层和变形协调三大难题,提出了四种典型的铺装结构,首次提出了钢桥面铺装设计参数和指标体系、铺装与钢箱梁整体优化设计技术,建立了钢桥面铺装设计方法,该方法已应用于之后建设的几十余座大桥。
随着铺装材料性能的不断改善和对铺装受力的研究深入,研究人员发现铺装的厚度和模量对于铺装层内部和层间的应力影响较大[66-80],并据此进行了组合铺装结构的相关研究。目前中国大跨径桥梁钢桥面铺装典型结构主要有4类:1) “双层环氧”结构,这种铺装方式强度高,耐久性能好,具有优异的高温稳定性能,如图9a所示;2) “浇注式+SMA”结构,采用这种铺装结构可以获得较好的低温稳定性,桥面系变形协调性能较好,但是在持续高温条件下易产生车辙病害,如图9b所示;3) “环氧EA+SMA”结构,这种铺装结构具有高强度以及优异的高温稳定性,低温稳定性良好且易于后期养护,如图9c所示;4) “浇注式+环氧EA”结构,这种铺装结构复合强度高,变形协调性及低温稳定性较好,如图9d所示。中国已有的桥面铺装工程实践表明,双层环氧铺装结构在适应超载和高低温稳定性方面表现最好,因而在工程应用中也最为广泛。表9总结了中国大跨径桥梁钢桥面铺装典型结构形式。
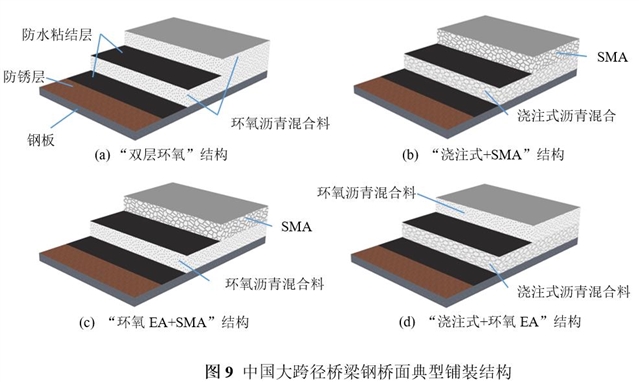
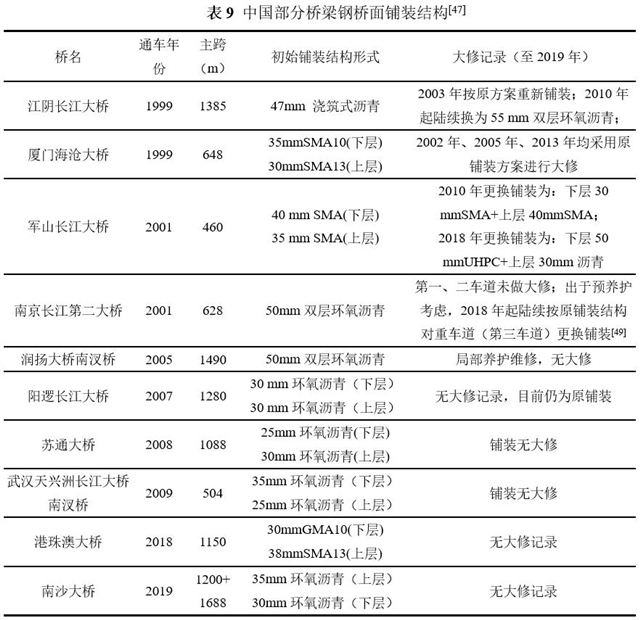
2.5 抗风设计
长江三角洲和珠江三角洲是中国大跨径桥梁最多的地区,这两个地区也是中国台风的多发区。受强风影响而产生的桥梁振动可能会引起桥梁构件过早疲劳破坏,严重的还会导致桥梁毁坏[81-82]。大跨径桥梁随着跨径的不断增大,结构相对较柔,风荷载对桥梁结构的影响也越来越大,因此,对大跨径桥梁的抗风设计提出了更高的要求。
经过多年的经验积累,中国的科研技术人员摸索出符合中国地理气候环境的抗风设计理论及风振控制方法。虎门大桥(1997年建成通车,主跨888m的悬索桥)是中国首个通过大尺度气动弹性模型风洞试验,对结构抗风性能进行系统研究的桥梁,从而保证了大桥的抗风性能满足要求。上海卢浦大桥(2003年建成通车,主跨550m的拱桥)在抗风设计中使用结构与气流相互作用的桥梁涡振等效风荷载计算方法,在国际上首次采用以涡振最长累计时间和首次发生涡振概率两个指标对桥梁涡振进行评价,并采用建筑膜结构进行涡振控制。在对西堠门大桥(2009年建成通车,主跨1650m的悬索桥)的抗风性能研究中,中国率先研发了系列桥梁颤振气动控制技术与桥梁涡振气动控制技术,对钢箱梁截面进行优化,采用间距6m的开槽双箱梁截面[83],发明了桥面侧向大风控制技术,研发了具有风-车-桥耦合振动分析功能的软件。
目前,中国已经建立了高精度桥梁气动力模型和风振分析方法,发展和完善了桥梁抗风设计理论;建立了大跨度缆索承重桥梁气动外形设计准则,提出了系统性的风振气动控制技术[84];研制成功“桥面开槽+气动翼板”组合的新型气动控制装置;自主研制了世界最大、性能先进的边界层风洞,为大跨度缆索承重桥梁抗风设计研究提供了关键技术装备。但基于抗风理论的目前实际状况,大跨径桥梁抗风设计尚难以摆脱对风洞试验的依赖、实现纯计算机数据的抗风设计。
2.6 抗震设计
中国地处欧亚地震带和环太平洋地震带之间,大多数地区属于地震多发区,因此中国历来重视大跨径桥梁结构的抗震设计。经过多年的理论和试验研究与工程实践,中国在大跨径桥梁抗震设计理论和桥梁减震隔震技术等方面取得了很大的进展。
在大跨径桥梁抗震设计理论方面,早期桥梁抗震设计主要采用静力理论或反应谱理论。随着对桥梁震害现象认识的不断提高,国内外研究学者认识到桥梁的抗震设计仅以生命安全和防止桥梁结构破坏为目标是远远不够的,基于性能的抗震设计理念应运而生[85]。基于性能的抗震设计理论能够考虑不同桥梁的结构特点和性能要求,综合运用桥梁的设计参数、结构体系、构造要求和减隔震装置来保障其在各级地震作用下的抗震性能。当前中国也与美国、日本、新西兰等国家一样将基于性能的抗震设计理论引入本国的抗震设计规范。地震动是桥梁抗震结构设计中一个重要的输入参数。当前桥梁结构抗震分析一般采用一致激励法作为地震动的输入方法,即假设桥梁基础各处的振幅与相位振动均相等,不考虑地震动空间变化的影响。但是对于大跨径桥梁,其结构为线性结构,地震动的空间差异性影响较为显著,目前主要通过多点激励的方式加以改进[11],但是总体而言,有关地震动空间差异特征的研究仍未成熟,是未来研究的一个重要方向。
在桥梁减震隔震技术方面,现有的工程经验表明,采用桥梁减隔震技术是减小桥梁地震灾害的一种行之有效的方法[86-92]。近几十年来,桥梁隔震技术研究集中在开发性能稳定且隔震效果良好的隔震支座,并给出相应的计算模型,通过优化支座参数,实现降低结构地震响应的目的。常见的桥梁隔震支座主要包括叠层钢板橡胶类支座和滑动摩擦类隔震支座。港珠澳大桥采用了新型高阻尼橡胶支座,该支座由多层高阻尼橡胶和钢板交替叠置而成,尺寸为1.77m×1.77m,是目前世界上最大的橡胶隔震支座,承载力高达3000 t,能协助桥梁抵抗8级地震作用[93]。滑动摩擦类隔震支座受地面运动频率的影响较小,具有承载力大、耐久性好、自恢复能力强等优点[94],受到桥梁工程师的广泛关注,在苏通长江大桥和上海长江大桥等桥梁中得到运用[95]。目前桥梁减震技术主要是通过主动控制、半主动控制、被动控制等方式,通过调整桥梁的刚度和阻尼特性,进而减小地震作用下的桥梁振动。其中,被动控制技术因具有可靠性高、维护成本低、研究理论较为成熟等优点而应用较为广泛。主动控制技术主要通过施加外部能量来改变桥梁的振动,具有较好的控制效率,但其可靠性没有保障,应用范围较为有限。半主动控制技术是目前发展前景较好的一种减震技术,能够综合主动控制技术和被动控制技术的优势,具有良好的可靠性和适应性,目前在多个桥梁结构中得到成功应用。
总体而言,中国的桥梁减隔震技术在过去取得了令人瞩目的研究进展,但仍存在许多亟待解决的技术难题。例如,橡胶类隔震支座的设计使用年限(一般为50年)与桥梁结构设计使用年限(一般为100~120年)不匹配,由于大跨径桥梁重量较大,橡胶类支座的服役寿命较短会给日后维护带来较大的挑战;隔震支座的稳定性和智能化等功能有待进一步提高;减震装置可能会改变桥梁结构的动力特性,进而影响桥梁结构抗震分析的准确性等。未来需要进一步研究并明确减震装置与桥梁结构的相互作用关系。
3 中国特大跨径桥梁的施工技术
3.1 基础施工
3.1.1 锚碇基础施工
陆地上重力式锚碇基础施工都需先开挖基坑,基坑开挖成功后再回填,浇筑基础与锚碇一体结构,基础开挖是个关键环节,辅以围护结构的开挖一般采用明挖法、爆破法和冻结法[96]等方法。常见的基坑形状包括矩形基坑、圆形基坑和“∞”形基坑,需要根据桥梁实际的建设环境选择合适的基坑形状。在大跨径桥梁锚碇基础施工实践中,中国取得许多创新性成果,具体包括研发了大落差混凝土输送防离析装置,发明了低强度、低弹模、低渗透性的自凝灰浆防渗墙,建立了基于空间弹塑性有限元理论的基坑结构分析模型等,相关技术达到了世界先进水平。
中国在隧道式锚碇施工方面也积累了很多成功的经验。例如,坝陵河大桥的隧道式锚碇在施工过程中面对开挖大倾角、大断面尺寸、洞室距离小、溶洞发育、岩体破碎等复杂建设条件,通过技术创新,创造性地提出45°大倾角锚塞体关键施工技术,与此同时,隧道锚碇上部还开展公路隧道开挖作业,建成后被誉为“世界第一隧道锚”[97],为中国同类型大跨径桥梁施工提供重要的指导。
3.1.2 群桩基础施工
群桩基础是桥梁最常用的基础形式,超过40%的桥梁采用桩群基础[11]。近年来,超流态混凝土、纤维混凝土和膨胀混凝土等新型绿色环保混凝土材料在群桩基础施工中的推广使用使得群桩基础的施工效率和质量得到了明显改善。
大型钢管桩基础因能克服复杂的地质、水文、气候条件、施工定位困难等难题,成为跨江跨海等大型水上桥梁常用的桩基形式,目前杭州湾跨海大桥、金塘大桥和东海大桥等均采用了大型钢管桩,钢管桩的直径达到2 m,桩身长度超过100 m,但是目前有关大直径钢管桩的理论研究相对滞后。
在灌注桩施工方面,目前中国最深的钻孔灌注桩基础己超过150 m,人工挖孔灌注桩直径已达到9 m,钻孔灌注桩直径达到5 m,相关的施工技术达到世界先进水平。大量的工程经验表明,采用压浆技术是提高钻孔灌注桩建设质量的有效途径,压浆是在钻孔桩施工完毕后,通过预埋在桩内的注浆管,向桩基端部或侧部注入可固化的纯水泥浆液来固化灌注桩的泥皮和沉渣,从而提高桩基的承载力和稳定性[11]。例如,苏通长江大桥在超长、超大的钻孔灌注桩施工过程中创造性地采用U型管压浆技术,使得桩基的承载能力提高48%~100%,该项技术为中国乃至世界桥梁桩基础的建设树立了成功的典范[98]。
3.1.3 沉井基础施工
沉井基础因具有整体性好、刚度大等优势,在大跨径桥梁基础中运用较为广泛,中国的南京长江第四大桥、江阴长江大桥和泰州长江大桥等均采用沉井基础。经过多年的桥梁工程建设实践,中国在沉井基础建设方面积累了丰富的经验,目前中国建成的沉井基础数量达数百座。在沉井基础施工技术水平方面,通过技术革新,中国的沉井基础施工技术位于世界前列,例如陆上建成的大型钢筋混凝土圆形沉井直径达68 m,最大下沉深度达57 m,平面面积达3600 m2。对于深水沉井基础,通过采用浮运沉井下沉方式,平面面积达数千平方米的沉井下沉深度超过50 m[99]。沪通长江大桥主塔基础尺寸达到86.9 m×58.7 m×115 m,成为世界上最大的沉井基础。面对未来跨江跨海的深水复杂施工环境,沉井基础与桩基等传统基础组合形成的复合基础将是未来大跨径桥梁基础建设的重要发展方向之一。
3.2 索塔施工
索塔按照结构材料可以分为钢筋混凝土索塔、钢索塔、钢管混凝土索塔以及钢-混凝土组合索塔,其中钢索塔与钢筋混凝土索塔由于施工简单而被广泛使用。
3.2.1 钢索塔施工
随着钢结构防腐技术的飞速发展,钢索塔因具有断面小、自重轻、强度高、韧性好、抗震性能好、施工工期短、施工质量易于控制、适应大跨径桥梁的变形等优势而受到工程界的青睐[100]。目前,中国已建成的大跨径桥梁包括泰州长江大桥、马鞍山长江公路大桥、南京长江三桥和杭州之江大桥等均采用钢索塔结构。相比于混凝土索塔结构,钢索塔结构的安装工序更为复杂[100]。要根据索塔的形状、高度、截面、重量,以及施工现场的地质、气候条件等来选择合适的施工方法。
经过多年的工程实践与理论研究,中国钢索塔的建设技术进入世界先进行列。例如,研发了钢索塔节段断面三维跟踪测量划线方法、具有曲线线形的桥梁钢塔柱曲线控制方法等技术,并成功应用于南京长江三桥钢索塔的建设,建成后的南京长江三桥钢索塔成为当时“中国第一座钢塔”和“世界第一座曲线钢塔”,并因此获得“古斯塔夫斯—林德恩斯”奖。
随后,中国在泰州长江公路大桥中针对中塔柱重1.2万吨、最大节段重量530吨和最大节段长15m的建设挑战,通过技术创新,成功攻克了现场焊接、安装精度控制、水平预拼等技术难题,图10为泰州长江大桥钢索塔施工安装照片,采用集节段制造、拼装与吊装于一体的全过程误差控制系统[30],成塔后的纵向垂直度和横向垂度分别为1/19591和1/50065,高质量地完成施工要求。
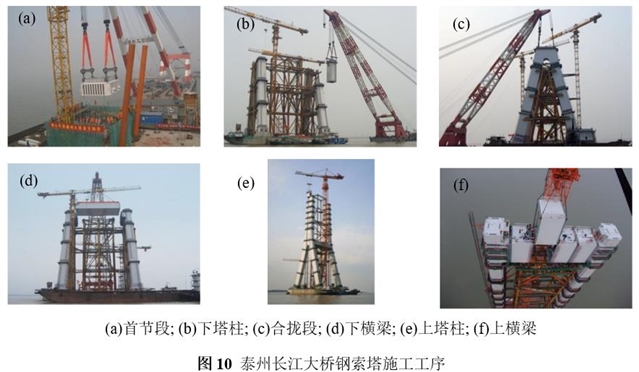
3.2.2 混凝土索塔施工
混凝土索塔是中国大跨径桥梁索塔的主要形式[101,102],对于塔身高、体积大的索塔工程,在混凝土索塔施工过程中,由于混凝土索塔的高度大,属于高空作业,所处环境较为恶劣,极易受到日照、降雨、大风等因素的影响,极易发生开裂病害,且会给模板工程的开展带来巨大的困难。此外,大跨径桥梁的施工周期一般较长,索塔结构的施工可能会经历不同的季节,其线形控制难度较大,再有索塔结构高且常常离岸远,施工测量精度难以保证,进而会影响到桥梁整体的施工质量[103]。针对上述施工阶段的技术难题,中国成功研发了混凝土桥塔液压爬模技术、混凝土超高泵送技术以及配套技术,目前中国大跨径桥梁混凝土桥塔的浇筑最大节段长度达6 m,爬模施工的效率得到明显的提高(12天/节,节高6 m),塔顶倾斜度误差可控制在1/42000内,远小于规范1/3000的要求,相关技术达到世界先进水平,为未来中国乃至世界大跨径桥梁混凝土索塔结构的建设提供了重要的技术支撑。液压爬模索塔施工照片参见图11。
索塔混凝土施工技术不仅是影响索塔结构服役性能的关键因素,还是影响索塔结构施工质量和效率的决定性因素。随着中国桥梁结构朝着超长、大跨、深水等方向发展,具有高强度、高流动性、低粘度和优异耐久性能等特征的高性能混凝土是未来索塔结构材料的发展方向。
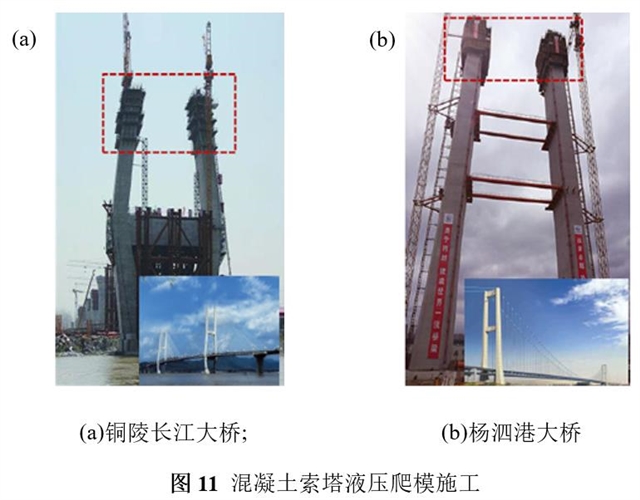
3.3 上部结构施工
3.3.1 钢箱梁制造
随着中国大跨径桥梁的发展,钢箱梁的宽度和长度不断增加,相关的板单元、零件数量相应增加。由于单件离散性偏差的绝对数量增多,钢箱梁整体的累计偏差变大[104]。为控制钢箱梁的整体质量和累计偏差,需要提高单元制造和单元组装的质量和精度。钢箱梁拼接完成后,其主要几何评价要素包括横截面尺寸、纵向制造线型、横截面相对错位及扭曲等三方面。中国钢箱梁制造技术“质”的进步主要体现在港珠澳大桥的钢箱梁制造上。
单元制造方面,港珠澳大桥钢箱梁U肋用钢板全部采用热轧平板,并冷弯成型。在以往项目中,冷弯U肋采用热轧卷板开平、切毛边后冷弯而成。由于卷板内外冷却速度不同,钢板两侧和中间的残余应力不均匀,切割下料后会出现较大旁弯,钢板平面度得不到有效保证。因此,冷弯U肋在制作过程中存在生产成本高、效率低等缺点,且在实际使用中存在疲劳等问题[105-106]。而港珠澳大桥U肋使用的热轧平板,由万能轧机一次热轧成型,钢板内部残余应力分布均匀,保证其质量和精度符合设计要求。同时,热轧平板的尺寸、刚度、强度、稳定性及抗疲劳性等性质与计算结果一致,利于相关标准的制定及规格型号的统一。
单元组装方面,港珠澳大桥箱梁组装定位首创性地采用U形肋板单元自动组装定位机床和板式加劲肋板单元自动组装定位机床(如图12所示)[106]。在此之前,我国钢箱梁组装定位多为人工为主,受人工因素的影响,U形肋与面板组装间隙、定位焊缝质量、U形肋中心距、直线度都受到很大影响,质量不稳定。而港珠澳大桥通过使用自动化定位技术,有效确保了组装时各部件的位置精度,避免焊接过程中因组装间隙较大所导致的U形肋根部烧穿的焊接缺陷现象[107],提高钢箱梁整体质量。
同时,港珠澳大桥在国内钢箱梁制造领域首次采用机器人焊接技术。中国大跨径钢桥发展之初,正交异性板单元的焊接通常采用人工焊接,焊接质量受焊工技术水平影响大;随着技术的进步,逐渐从人工焊接发展为焊接小车或龙门式多机头组合焊接小车的方式,但仍然需要人工随时对焊丝位置进行修正调整。受U形肋加工偏差、直线度的影响,焊丝往往因跟踪偏差而偏离坡口根部,导致焊接熔池偏离,很难确保焊接熔深的稳定性[106-107]。而港珠澳大桥在日本神钢ARCMAN-MP型焊接机器人系统的基础上,研制了正交异性板单元多头焊接专用机床(如图13所示),能够对焊接熔池零距离实时跟踪,实现对坡口根部实时精确跟踪,有效地保证坡口根部焊缝的熔合和熔透深度,焊接质量更稳定。
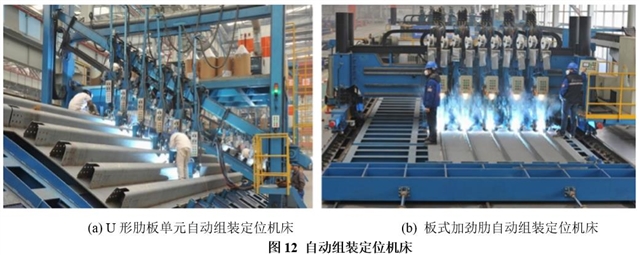
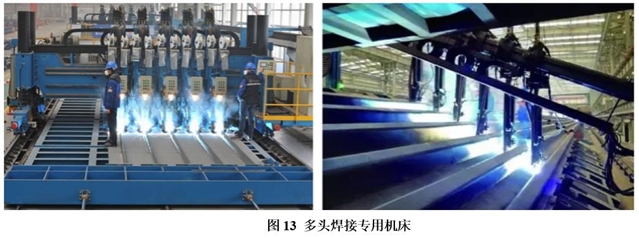
3.3.2 主缆及主梁施工
主缆是悬索桥的生命线,从目前的施工技术来看,桥梁一旦建成主缆就不易更换,所以主缆的施工质量对桥梁结构的安全至关重要。大跨径悬索桥主缆在施工中处于下挠的状态,为避免出现索股扭转、鼓丝、散丝、绑扎带断裂等情况[104],施工中需要对主缆架设的精度和质量进行严格控制。国内的悬索桥主缆普遍采用预制平行索股法架设,其主缆牵引系统在锚碇端安装两台绞车, 牵引绳通过猫道滚轮从前往桥梁另一侧,转向后经由同一猫道的另一侧滚轮回到起始一侧。牵引系统需要有适当的后张力, 保证牵引索具有连续、平顺的线形, 避免在拽拉器处发生折弯或下垂现象[108]。汕头海湾大桥是中国首座采用轨道小车式牵引系统架设主缆的桥梁;随后改进了施工工艺,在江阴长江大桥施工时采用了架空索道式牵引系统;在成功应用于海沧大桥与虎门大桥后,门架拽拉器式牵引系统的施工方式在国内被广泛应用,之后建成的宜昌长江大桥与忠县长江大桥也采用了这种施工方式。在润扬长江大桥的建设过程中,结合现场实际情况,将牵引系统改进为双线往复式,提高了主缆架设效率,加快了施工进度。
在主梁施工方面,中国掌握了混凝土梁整孔预制架设技术、梁上运梁架设技术、匹配法预制拼装施工技术、钢箱梁整体吊装施工技术和使用缆载吊机、桥面吊机、顶推与滑模等主梁架设与施工技术,自主开发了浮吊、架桥机、桥面吊机、缆载吊机、大型龙门吊、滑模设备等关键装备,其中缆载吊机吊装能力(740 t/段)和转体施工技术(转体长度198 m,转体重量22400 t),达到了国际领先水平。顶推法是钢箱梁架设的主要施工方法之一,按照动力装置数量分为单点顶推和多点顶推。2005年建成的洪山庙大桥是我国第一座采用顶推法施工的钢箱梁斜拉桥,在此之后,中国钢箱梁顶推技术飞速发展,最大顶推跨径不断提高,适用的桥梁型式也从直线桥发展为曲线桥,从等截面梁发展为变截面梁[109]。
由于主梁和缆索间密切的传力关系,施工中需要统筹兼顾两者的架设。悬索桥方面,虎门大桥在国内首次成功地设计、制作、架设了每股127丝的大型预制索股,并开发出一套完整的先进施工工艺和专用设备;同时研发卷扬式、液压式跨缆起重机将所有钢箱梁吊装就位[110],并率先采用钢箱梁节段间全焊连接的结构形式,解决了焊缝间隙调整工艺和焊接技术问题。斜拉桥方面,苏通长江大桥边跨、辅助跨以及索塔区的大块梁段采用浮吊整体吊装,标准梁段采用桥面双吊机系统进行吊装,中跨合龙采取顶推辅助合龙方法[111]。同时,苏通长江大桥在国际上首次系统提出了千米级斜拉桥施工全过程自适应几何控制方法,并建立了制造安装一体化程序,创造了斜拉索与钢箱梁数字化安装控制关键技术,实现了长索制作精度提高到1/20000、主梁标高误差≤L/4000、桥轴线误差≤L/45000,攻克了千米级斜拉桥施工技术难题。
3.3.3 拱桥主拱施工
混凝土拱桥主拱施工方法分为有支架、无支架两种,采用哪种方法取决于在施工过程中主拱是否将已完成的结构作为支撑体系。拱桥跨径的突破与施工技术密不可分。目前在混凝土拱桥的施工中也采用了缆索吊装、转体施工、斜拉扣挂和劲性骨架施工等方法,大大提高了混凝土拱桥的施工效率和质量[112]。
斜拉扣挂法是大跨径钢筋混凝土拱桥采用最早、最多的无支架施工方法,要点是先在拱脚墩、台处安装临时塔架,用斜拉索一端拉住拱圈节段,另一端绕向台后并锚固在岩盘上,然后逐节悬臂施工直至主拱拱顶合龙[109]。斜拉扣挂工艺需要使用斜拉索,当主拱的跨径很大时,需解决拉索的自重与垂度问题,可采用轻质高强的碳纤维复合材料拉索,并使安装更加便捷。
劲性骨架法用于大跨径拱桥,大幅提高了混凝土拱桥的跨越能力,原因是其将较重的混凝土拱的架设问题转化为较轻的钢骨架拱的架设[114]。劲性骨架从型钢向钢管混凝土发展,使混凝土拱桥跨径取得进一步突破。万州长江大桥是世界首座跨度大于400m的钢筋混凝土拱桥[114-115],以钢管混凝土为劲性骨架,以C60高强混凝土为拱圈材料,采用了大吨位多节段缆索吊装悬拼扣锚安装工艺[116-117]和拱圈混凝土长距离大落差两级泵送对称浇注工艺[118]。2013 年建成的合江长江一桥是世界上第一座跨径超过500 m的钢管混凝土拱桥,实现了特大跨径钢管混凝土拱桥管内混凝土全过程真空辅助三级连续泵送施工[119]。钢管拱桥在我国的成功,特别是千斤顶、液压技术、计算机技术、测试技术等的综合运用,整体提升了大节段钢拱的安全性。在钢管混凝土拱桥的施工中,拱肋的施工精度和施工稳定性问题受到高度重视,主要包括钢管骨架架设与合龙时的稳定问题和后续加载过程中的稳定问题。当跨径较大或采用钢管混凝土作为施工劲性骨架时,考虑到结构刚度较弱,需要进行考虑大变形的稳定分析。
大跨径拱桥转体施工技术在特定的地理环境下具有独特优势。球铰是实现转体技术的关键,常用的材料有钢材和混凝土。目前国内钢制球铰的最大转体质量是沪杭高速铁路跨沪杭高速转体桥,转体质量达16800 t [120]。转体施工结构为了增大跨度而选择采用劲性骨架,结构的稳定性必然降低。为避免转体阶段可能发生的结构失稳,在施工转体前应进行转动体称重试验,测试转动体部分的不平衡力矩、摩阻力矩、偏心距等。
3.4 钢桥面铺装施工
钢桥面铺装技术是桥面铺装材料设计、结构设计、施工等环节层层相扣并成套的复杂技术。一些铺装材料在室内试验中表现出良好的性能,但实际运用到桥面上时,却由于施工技术不完善或施工质量控制不严而调整的材料配比、摊铺温度和时间等因素,导致桥面铺装未达到预计使用性能。因此,结合室内试验,正确设计施工方案和质量控制体系是保证铺装成功的重要环节。
3.4.1 环氧沥青混合料铺装施工
环氧沥青混合料的控制指标较多,施工要求严格,原因是施工过程中环氧树脂快速固化,环氧沥青混合料桥面铺装对结构和环境有很强的敏感性。一般的环氧沥青钢桥面铺装方案,工艺流程可分为备料、配合比设计、喷洒防水粘结层、混合料生产与运输、下层摊铺与碾压、接缝处理、喷洒粘结层、混合料生产与运输、上层摊铺、碾压、接缝处理、养护等12个环节。近年来,国内的环氧沥青混合料制备工艺从热拌法发展到温拌、冷拌,开发低温施工技术,铺装技术呈现多样化的发展方向[121]。目前国内已经出台《公路钢桥面铺装设计与施工技术规范》(JTG 3364-02-2019)等规范和标准,以指导环氧沥青混合料铺装的设计与施工[122]。
对于温拌型环氧沥青混合料,关键铺装工序如下:(1)拌合与运输:环氧树脂施工前温度控制在80℃ 左右,固化剂与沥青混合物拌合前温度控制在150℃,环氧沥青混合料出料温度宜为110℃ ~ 120℃。(2)摊铺:施工前应对摊铺机进行预热,温度控制应与出料温度相近。(3)碾压:严格遵守初压、复压、终压的施工工序。初压必须紧跟摊铺工序,并确保初压终了温度≥82℃,终压终了温度≥65℃。将固化试件空隙率≤3%、稳定度≥40 kN作为确定混合料施工容留时间的控制指标[59]。(4)养护:在施工完成后铺设保温材料,养护期间封闭交通,铺装达到通车要求的强度指标为马歇尔稳定度≥40 kN。
不同于温拌型环氧沥青混合料,热拌型环氧沥青的黏度随温度升高而逐渐下降,黏度增长的速率随时间迅速减小。该特性延长了混合料的摊铺时间,因此热拌环氧沥青混合料的施工时间更灵活[123]。热拌型环氧沥青混凝土早期强度增长快,一般只需养生数天即可开放交通。黄红明等研发的新型国产环氧沥青混合料(N-EA)具有宽泛的施工温度和时间控制范围,混合料在165℃~185℃容留温度下的施工时间可达3h,并在40℃温度条件下养生4天后马歇尔稳定度即高于50kN,达到开放交通的强度要求[124]。
总体而言,环氧沥青混合料在成型温度、时间、成型工艺和压实等方面较其他混合料技术要求更为严格,在工程实施中要予以足够的重视。选择合适的制备工艺,严控温度、时间、压实度和空隙率,对于桥面铺装的成功实施至关重要[125]。
3.4.2 浇注式沥青混合料铺装施工
浇注式沥青混合料具有沥青用量高、矿粉含量高、拌和温度高的特点,可以采用浇注自流成型的摊铺工艺,常作为下层铺装材料。根据生产工艺特点,浇注式沥青混合料可以分为Guss Asphalt(GA)和Mastic Asphalt(MA)两种类型,其主要的特点如表10所示:

浇注式沥青铺装技术于20世纪90年代首次引入国内,并在江阴长江大桥、中国香港青马大桥应用,两座大桥均采用了英国铺装技术(MA),铺装结构为单层浇注式。由于受苛刻交通、气候条件影响,单层浇注式铺装的实际效果并不理想。此后,国内的钢桥面铺装工程基本采用浇注式沥青混合料双层铺装结构,铺装下层为浇注式沥青GA,上层多采用改性沥青SMA [127]。
港珠澳大桥是目前国内钢桥面铺装面积最大的单体工程,采用浇注式沥青混合料+改性沥青SMA铺装结构。在铺装实施过程中,引进大型车载式抛丸机,开发全断面自动喷涂系统,解决了钢板喷砂除锈作业工效低的问题。为了实施经过设计优化的MA浇注式沥青铺装方案,提出了独创的GMA工艺,实行精细化集料加工技术,保障原材料稳定性。采用基于无核密度仪的压实度检测方法,以得到路面施工是否合格的依据[128]。GMA工艺结合了GA和MA的两种特性,但二者的评价方法不尽相同:GA一般采用贯入度或贯入度增量来评价其高温稳定性,用流动度来评价其施工和易性;MA通过硬度值、马歇尔稳定度、流值评价其高温稳定性。港珠澳大桥综合两种评价方法,采用车辙试验评价浇注式沥青混凝+GMA的高温稳定性,采用冲击韧性评价疲劳性能。质量验收指标如表11~12所示:
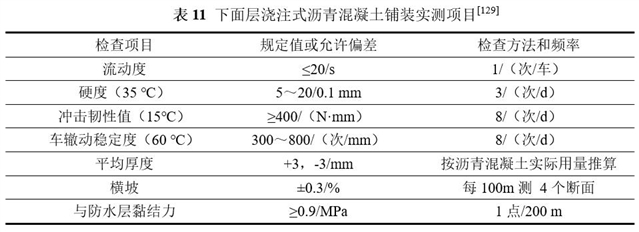
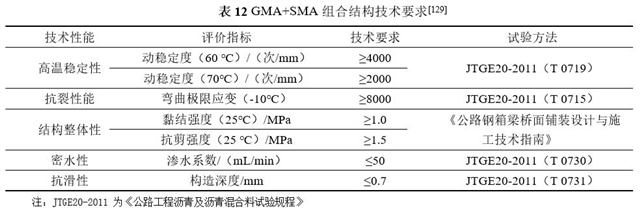
4 中国特大跨径桥梁的使用状况
随着服役年限的增加,不少大桥受施工、气候、交通及养护等因素的影响,出现了一些损伤。其病害主要包括钢箱梁焊缝及母材开裂、桥面铺装裂缝、拉索护套破损、锚头锈蚀、支座损坏以及索塔的损坏等。这些病害影响桥梁的运营能力,带来桥梁结构安全风险。
在收集相关资料的基础上,作者于2018年下半年对多座代表性桥梁进行了调研,实地查看桥梁的使用状况,特别是钢箱梁的情况,取得了宝贵的现场资料。
4.1 钢箱梁使用状况
4.1.1 钢箱梁病害
通过对大跨径桥梁钢箱梁内部病害的检查和总结,发现钢箱梁病害以开裂、锈蚀以及涂层脱落为主,其中开裂病害最普遍,往往占钢箱梁病害总数的80%以上,且分布广泛。受服役年限和交通压力影响,早期建成的大跨径桥梁钢箱梁内裂缝数量逐年增长,发生在箱梁内的各个部位,参见图14。表13为中国某大跨径桥梁钢箱梁内的裂缝统计,可以发现,2017年较2015年新增裂缝约85%,且已补焊过的裂缝仍有重新开裂的现象。
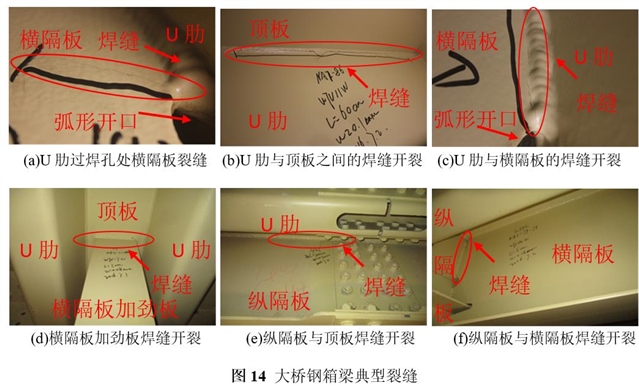
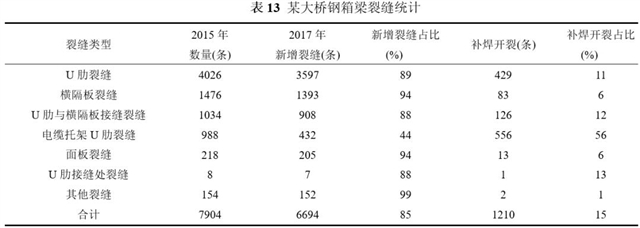
钢箱梁病害原因主要有内因和外因两种:内因包括设计缺陷、施工缺陷、母材及构造缺陷等;外因包括重车荷载、大交通量、养护不及时等。根据多个大桥钢箱梁病害总结,发现钢箱梁内裂缝的分布和发展有以下规律:1) 多发生于构件焊缝连接处,例如U肋与顶板焊缝、U肋与横隔板焊缝等,其中U肋与顶板焊缝的内侧病害最难观察,少数大桥的病害发生于母材;2) 多发生于重车道下方;3) 纵桥方向上,病害多集中于跨中、边跨以及上坡段;4) 钢箱梁开裂病害多发处与铺装病害多发处对应;5) 一般通车10年左右开始出现病害,并根据体系和地区的不同以及维护水平情况,在未来可能存在爆发性增长。
4.1.2 钢箱梁裂缝修复措施
由于钢箱梁的裂缝产生机理不同,其治理模式也应根据不同的裂缝原因制定针对性的措施,不能只简单的采用补焊方式。
1) 对于桥面板裂缝,宜采用将桥面板上方的铺装层刨除后,下垫陶瓷衬垫补焊的方式进行修复;为了完全修复裂缝,需采用超声波法与探孔法探明隐性裂缝的位置、长度及发展方向等。
2) 对于U肋与桥面板焊缝处的裂缝,通过探孔检查确定裂缝起始和终止位置后,宜从尖端位置将原有开裂焊缝全部刨除后进行补焊处理。
3) 对于U肋裂缝,当裂缝长度较小时,可在裂缝尖端设置止裂螺栓孔,利用高强度螺栓拧紧,限制裂缝的发展;当裂缝长度较大时,在裂缝处垫加强钢板,并用高强螺栓沿裂缝位置夹紧。
4) 对于横隔板弧形开口裂缝,可采用打止裂孔或栓接补强板的方式进行维修。
4.2 斜拉索使用状况
4.2.1 斜拉索病害
斜拉索损伤的原因主要分为人为因素和环境因素两类。人为因素:由于斜拉索施工涉及的工序较为繁杂,且护套保护层是柔性聚合物,因此在涉及斜拉索的作业中会受到一定程度的损伤;环境因素:受车载、风载、雨载及雪载等可变荷载的共同作用,拉索应力变化大,且往复性的伸长量变化使得拉索或护套出现疲劳裂缝,破坏防护系统的整体性。如图15所示,典型的斜拉索病害有护套刮伤、将军帽锈蚀、套筒渗水锈蚀、阻尼器漏油以及锚具保护盖缺失等。
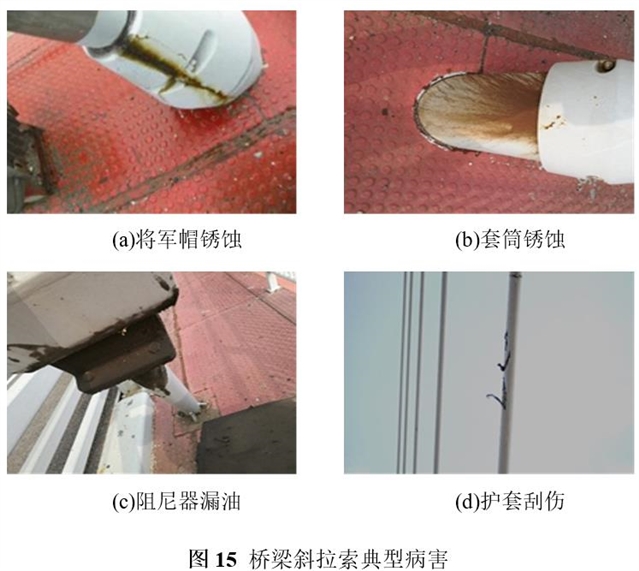
4.2.2 斜拉索修复措施
斜拉索护套的破坏分为轻微损伤、深度损伤与严重损伤三个等级,对于不同程度的损伤应采取相应的修护措施。对于表面结垢或划伤等轻微损伤,可采用中性水清洗以及表面打磨处理。对于表现为明显开裂的深度损伤,应将护套破损处周围的污秽擦干净,用美工刀沿破损周边切割PE护套并露出破损处钢丝,用挤出式塑焊枪将相同原料焊接于护套开窗处,如图16a所示,之后用磨光机打磨修补表面,使损坏处恢复到原有及平整状态,如图16b所示。对于护套严重开裂并露出钢丝的严重损伤情况,修复方式如下:检查斜拉索两端防水系统,了解锚头锈蚀情况并排出锚固端积水,对拉索内部进行充分干燥;将护套破损处周围的污秽擦干净,确保修补时不影响护套之间的粘连;用美工刀对病害处PE护套开窗检查;采用钢丝刷和砂纸打磨除锈,然后涂刷防腐剂(富锌底漆+环氧云铁封闭漆);对钢丝表面用聚酯带进行双层缠包,如图16c所示;用挤出式塑焊枪将相同原料焊接于PE护套开窗处。用磨光机打磨修补表面,使损坏处的护套恢复到原有及平整状态。
斜拉索将军帽接缝常因积水产生侵蚀,长时间后涂层退化、破坏造成将军帽材料锈蚀,影响密封性,此外橡胶条老化也会导致功能下降。对于此类病害,可以采取打开将军帽后对内部的结构锈蚀进行除锈处理的措施;如内部存在积水,在拉索下锚头位置开孔,将内部积水清除,之后全部更换全新将军帽及填充料。
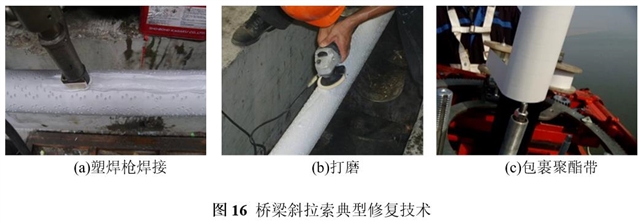
4.3 索塔及支座使用状况
4.3.1 索塔及支座病害
索塔作为缆索承重体系桥梁的主要承力结构,混凝土塔柱的竖向及横向裂缝、节段裂缝以及混凝土的破损是其主要病害。以某大桥为例,一次桥梁检测时,在一个塔柱上发现124条竖向裂缝,77条横向裂缝,9处网状裂缝;在另个塔柱上共发现121条竖向裂缝,26条横向裂缝,7处网状裂缝。
支座病害主要为支座涂层锈蚀、限位支座钢板变形开裂、竖向支座滑动面磨损严重、填充物大量挤出等。限位支座变形开裂有可能是由于支座锈蚀或橡胶老化等原因造成支座性能下降不满足梁体位移变化或受力要求等造成。竖向支座病害原因分为两方面,一方面是盆式橡胶支座老化锈蚀,养护、除锈措施不到位;另一方面是车辆及温度等外加荷载的长期作用,导致四氟板磨损严重,大量填充物被挤出。
4.3.2 索塔及支座修复措施
混凝土索塔病害属于常见混凝土结构病害,可采取裂缝封闭、灌浆、混凝土缺损修补或者必要时采取粘贴钢板或复合材料等加固措施进行处置。
对于磨损、锈蚀严重的支座部件应进行更换。某大桥的支座更换工程采用了计算机同步顶升控制系统,以墩为单位,左右支座同时分级顶升,以保证顶升的同步性。顶升的高度受到严格的控制,在梁被顶升20mm后,立即架设辅助支撑,确保每个临时支撑均匀受力。以冷切割的方式切除支座所有连接螺栓取出旧支座。在对安装位置混凝土表面进行清理之后,即可进行新支座的定位安装。落梁时,先将梁体向上顶起1mm后再拆除临时支撑,缓缓落梁并就位,完成支座更换。
4.4 钢桥面铺装使用状况
4.4.1 桥面铺装病害
重载车辆以及繁重的交通量与恶劣的高低温条件是中国钢桥面铺装层破损的主要原因。从断裂力学角度来看,钢桥面铺装层实际铺设过程中总是会在表面留下许多细小的缺陷, 随着轴载作用次数的增加,铺装层结构会发生不同程度的损伤, 且在不同的使用阶段,相同的荷载对铺装层所造成的损伤是不同的。某大桥设计日均流量为8万辆,而现在日车流量已超过10万,高峰时期甚至达到14.24万,该大桥铺装病害主要集中于重车道和跨中区域。由于铺装材料和交通荷载的原因,某大桥的浇筑式沥青铺装层通车一年内就发生了深5mm~8mm、长200 m左右的塑性变形,并有发展为车辙的趋势;通车两年内,车辙处就产生长0.5m~2m、宽1mm~3mm的裂缝。
从地域来看,亚热带季风气候区是钢桥面铺装层严重病害的多发地,该地区高温持续时间较长,5~10月平均最高气温达到33℃~37℃。对于位于南方城市的大跨径钢桥,夏季钢桥面铺装层表面温度最高可达70℃,昼夜温差最大超过30℃,这更加剧了铺装层材料的破坏。
根据对多个大桥的铺装病害进行总结,发现有以下规律:1) 多发生于轮迹带和重车道;2) 不同车道的连接处易形成纵向裂缝;3) 纵桥方向上,病害多集中于跨中、边跨以及上坡段,支座附近病害较少;4) 病害多发处与钢箱梁病害多发处对应;5) 存在爆发性增长现象,时间点一般为大桥通车7~10年左右。
4.4.2 桥面铺装修复措施
桥面铺装经历一段服役期后将不可避免发生不同程度的破损。根据不同的破损情况和交通量状况,桥面铺装一般可采取预防性养护、修复性养护和翻修三种修复处理措施。
预防性养护是在桥面铺装出现明显病害之前而采取的主动性养护措施,目的在于延缓桥面铺装的破损进程,延长其服役使用寿命。常见的预防性养护措施包括裂缝填封、雾封层和微表处等[130]。工程经验表明,预防性养护是桥面铺装修复养护工作最重要的组成部分,效益高,成本低,是保证实现铺装设计目标和铺装正常使用的关键环节,应受到足够的重视。
修复性养护主要指的是对桥面铺装局部出现的坑槽、裂缝、推移等病害进行修复,按目标修补寿命一般可分为应急性修复、半永久性修复和永久性修复。常见的修复性养护技术包括就地热再生技术、厂拌热再生法、就地冷再生法和雾封层技术等[131]。
当桥面铺装发生大面积破损,采取修复性养护已无法遏制病害的发展时,需要对桥面铺装采取翻修措施。桥面铺装的翻修,即去除原有的桥面铺装,重新对钢桥面进行防锈防水等处理,再摊铺新的铺装层,一般需要根据桥面交通量状况、环境条件、施工条件和经济社会效益等方面来综合确定翻修方案。
5 中国特大跨径桥梁设计技术的进步与展望
5.1标准体系
大跨径桥梁的标准体系是体现国家桥梁工程建设水平的重要指标,是桥梁建设经验的高度总结。大跨径桥梁由于其结构的重要性,在设计和施工方面常常需要根据实际情况采取突破常规的技术方法,只有经过工程实践验证的成熟的设计和施工技术,才有可能形成标准体系,对国家的大跨径桥梁建设形成技术要求。根据近几十年来大量桥梁工程的建设经验来看,中国桥梁设计的标准体系和标准规范面临着需要不断丰富和完善的形式和任务。2002年,中国发布了《公路工程行业标准体系》(JTG A01-2002),并陆续建立了涵盖约80本标准的JTG标准体系(现行为《公路工程标准体系》(JTG 1001-2017)),还制定了《公路悬索桥设计规范》(JTG/T D65-05-2015)、《公路斜拉桥设计规范》(JTG 3365-01-2020)和《公路钢管混凝土拱桥设计规范》(JTG/T D65-06-2015)等专项设计规范,这些对中国大跨径桥梁设计起到重要的指导作用。但是中国还没有建立国家层面的大跨径桥梁设计标准体系,也缺乏相应的国家层面的标准和规范。中国在承接海外大跨径桥梁设计任务后,常常是借用欧洲和美国等国外规范。对比国外发达国家来看,中国大跨径桥梁的设计技术标准体系是滞后于实际工程建设的,国家层面上的标准体系仍十分欠缺。因此,加快完善中国大跨径桥梁结构标准体系建设,是当前及今后较长时间内的一项紧迫任务。
为了建立一个完善的特大跨径桥梁设计技术标准体系,应当面向当下和未来,审慎思考,引入国内外先进的桥梁设计理论,充分吸纳中国近几十年来积累的成熟建设经验,剔除不正确或不成熟的设计概念,另外,还应当关注和桥梁建设息息相关的行业或专业,例如高速发展的材料科学、计算机技术和不断更新换代的工程装备,并充分认识到“建养并重”的重要性,研究桥梁建成之后的管养技术,包括健康监测、评估和维护,以确保桥梁运营和结构安全。
5.2 高性能材料
特大跨径桥梁的设计方案在很大程度上取决于桥梁结构用钢的发展,中国的桥梁结构用钢大致经历了“碳锰钢→低合金钢→高强钢→高性能钢”的发展阶段[132]。目前,中国《桥梁用结构钢》(GB/T 714-2015)标准给出了Q345qNH~Q550qNH牌号高性能钢的技术指标,但总体而言,中国桥梁高性能钢材的标准编制落后于桥梁发展需求。此外,随着新型桥梁高性能钢的不断研发,桥梁构件的焊接选材、工艺以及质量的指标要求也需及时更新调整,以提高二者使用的匹配度。近年来中国大跨径桥梁设计越来越重视绿色与可持续的理念,可以预见未来大跨径桥梁高性能钢将具有广阔的发展空间。
特大跨径桥梁的缆索主要由钢丝组成,作为桥梁的重要受力构件,其质量直接关系到桥梁的安全性和耐久性。经过多年的研究,中国在特大跨径桥梁建设中普遍使用了1860 MPa的高强钢丝与高强钢绞线,在建的斜拉桥的斜拉索与悬索桥的主缆也采用了最新研制的1960MPa~2000 MPa的高强钢丝[133]。中国的高强钢丝形成了具有自主产权的完整生产工艺体系,且性能指标优于国外同类产品[134]。
但是,现有的桥梁养护规范尚未建立缆索寿命的评估方法,导致缆索的后期维护方案无据可循[135]。这给桥梁设计因考虑后期维护而选择材料时带来了困难,目前桥梁管养部门一般采取发现拉索锈蚀严重即更换的措施,这可能会造成不必要的浪费。尽管目前国内学者针对高强钢丝锈蚀寿命开展了一些研究[136-138],但是相关研究仍十分有限,未来需要对高强钢丝的锈蚀规律与力学性能衰减规律开展深入研究,并据此建立缆索服役寿命的评估方法。
当前中国绝大多数大跨径桥梁的桥面铺装采用环氧沥青混合料、浇注式沥青混合料及沥青玛蹄脂碎石等沥青混合料,由于中国幅员辽阔,不同地区大跨径桥梁所处的服役环境状况以及交通状况存在较大差异,对桥梁的实际需求也不同,这些都会影响桥梁的设计方案。随着材料的发展,未来会出现更轻、更薄、更耐用的铺装结构,不但提高了桥面铺装层与钢箱梁受力与变形的兼容性,还可减小大跨径桥梁的自重,将促进大跨径桥梁结构型式的设计创新,进一步提高大跨径桥梁结构的设计跨径。
5.3 信息化技术
随着物联网技术的发展,大跨径桥梁建设的信息化技术应用已成为加快发展的重要手段。
在桥梁设计软件方面,经过30多年的研发与应用,中国实现了从无到有、从有到优的发展,中国自主研发的桥梁辅助设计与分析软件已经取得了较大的进展。应用较广泛的国产设计分析及施工控制软件包括桥梁博士、QJX、GQJS、PRBP、BINAS、桥梁大师和方案设计师等,计算精度与效率与国外同类软件基本相当。且与国内规范及实际工程结合度较高[139]。
BIM (Building Information Modeling)技术在中国桥梁设计、施工和养护[140]阶段得到了初步的应用[141-143]。通过BIM协同管理,中国大跨径桥梁已经实现了架设自动化控制和吊装运行状态控制等智能建造技术[144],保证了桥梁建设的安全性、高效性和可控性。港珠澳大桥工程建设中,已试行了钢箱梁的智能制造[139]。通过BIM协同管理,中国大跨径钢桥还摆脱了传统的人工监测,开始使用自主设计的AI健康监测系统,利用传感器物联网[145]、云计算[146]、大数据处理[140]等信息技术,提高监测效率和可靠性,保证大桥安全。当前桥梁BIM标准的编制、桥梁BIM软件的开发以及相关的工程应用的示范等BIM技术的试点工作正在开展。
总体而言,中国大跨径桥梁的设计已经开始应用智能建造、AI监测等信息化技术,但目前仍处于起步阶段,技术水平未能满足实际工程全生命周期内的各项需求。此外,设计软件的研发仍是中国大跨径桥梁建设发展的一个短板,未来需要注重研发适用于大跨径桥梁复杂力学行为分析的国产核心软件。同时,中国需要研发实用的国产BIM软件,建立大跨径桥梁BIM标准体系,兼顾大桥的规划、设计、施工、养护、管理等全生命周期,实现大桥全生命周期的信息化管理。
5.4 工程装备
更先进的工程装备能够为桥梁的设计方案提供更多的可能性。结合中国大跨径桥梁建设的基本情况,在引进和消化国外先进建设技术和工程装备的基础上,中国在桥梁基础、桥塔、缆索、主梁建设等工程装备方面取得了突破性的进展[134,147]。
总体而言,中国目前在打桩船、起重机、缆载吊机等一些大型工程装备方面实现了自主研发,大幅减少了工程租赁费用,且设备的使用性能达到世界先进水平。但是,这些装备的可靠性和服役寿命相比于国外同类设备仍存在一定差距。一些装备的关键核心部件依然严重依赖进口,不具备自主生产能力。未来需要研究并提升大跨径桥梁建设工程装备的可靠性及关键部件生产能力。
5.5 健康监测与评估
大跨径桥梁应进行结构健康监测系统设计。大跨径桥梁健康监测系统一般可分为传感器系统、数据采集和传输系统、数据处理和控制系统、结构健康评估系统、检查维护系统等5个子系统,具备结构监测、环境监测、交通监测、设备监测、损伤识别、整体性能评估、综合报警、信息网络分析处理与桥梁养护管理等功能[148]。中国的桥梁健康监测研究起步相对较晚,自上世纪90年代起,中国才陆续建立了不同规模的健康监测系统,国内学者通过研究建立了相关的数据分析和评估理论、方法和技术体系[149-150],为评估桥梁结构的服役状况、验证大跨径桥梁的理论模型、完善大跨径桥梁的设计理论提供重要的数据和理论支撑。
虽然目前中国很多大跨径桥梁均建有不同规模的健康监测系统,但是实际上大多数仍处于研究状态,这导致大跨径桥梁的结构设计、施工管理与运营维护有所脱节。大跨径桥梁健康监测指标众多,实时积累的原始数据以海量计算,这给原始数据的存储带来巨大的挑战。当前监测数据仍缺少标准化、规范化的分析系统。此外,各类传感器的稳定性较差,且使用寿命相比大跨径桥梁寿命短的多,更换困难,这都导致健康监测系统无法充分实现预期目标甚至处于完全瘫痪的状态。因此,未来需在耐久、可靠、稳定的传感器系统开发、原始数据的有效保存与分析、监测指标与桥梁服役性能的关联等方面开展深入的研究工作,并建立相应的国家标准规范,实现设计、建设、运营一体化管理。
5.6 未来桥梁设计方向
5.6.1 特大跨径海上桥梁
中国东部临海,岛屿众多,随着经济社会的发展,未来中国仍有建设大型甚至特大型跨海桥梁的需求。中国现行的桥梁设计标准规范仅适用于跨径小于2000m的悬索桥[151]和跨径小于1000 m的斜拉桥[152],且设计使用年限为100年,不适用于特大型跨海桥梁的建设。虽然目前欧洲、日本和韩国已经针对主跨为1200m~1600m的双塔斜拉桥、主跨为2700m~3300 m的悬索桥、主跨为1400m的协作体系桥开展了技术研究和探索应用[147],但是目前世界上已建或在建的大跨径桥梁均小于2000m,国内外尚无特大型跨海桥梁设计与建设经验可循。因此,未来需要结合大跨径桥梁的科研和现场资料,针对特大型跨海桥梁开展基础和应用研究,建立一套完善的设计技术标准,为将来在复杂环境条件下建好桥梁打下坚实基础。
5.6.2 高速铁路大桥
目前中国高速铁路建设发展迅速,大跨度铁路桥梁的建设需求也越来越强烈。与公路桥梁不同,由于列车运行速度较快,大跨度铁路桥梁承受的活载作用大,车桥系统的动力作用非常明显,对桥梁结构的刚度要求较高。此外,大跨度高速铁路桥梁不仅需要保证列车行驶的安全性,也要满足行车的舒适性[153]。中国针对公铁两用大跨径斜拉桥的结构动力响应[154-155]、桥面铺装受力特征[156]、抗震减震[157-159]、车桥耦合振动[160-161]等方面开展了一定的研究,且相关成果在实际工程中得到了应用。当前有关公铁两用大跨径悬索桥理论研究也主要集中在公铁两用大跨径悬索桥抗风、抗震等性能的研究[162-163]。
总体而言,高速铁路大桥在中国发展仍处于起步阶段,相关的设计理论仍不完善,未来仍需在高速铁路大桥荷载分布特征、桥梁结构刚度和稳定性、桥梁结构优化等方面开展基础理论研究,建立和完善相关的设计标准体系,指导高速铁路大桥的建设。
6 结语
中国特大跨径桥梁的设计与建设取得了极大的进步和发展,本文总结了近三十年来中国大跨径斜拉桥、悬索桥和拱桥的基本情况,综述了设计及建设技术的进步,调研了目前的使用状况,并对中国特大跨径桥梁的设计方向进行了展望。未来,中国特大跨径桥梁设计应结合近几十年来的设计、建设经验,除考虑生命周期、结构安全、建设规模外,还应考虑到美观、舒适及后期的健康监测和维护等需求;同时还需要建立国家层面上的统一标准,并在特大型跨海桥梁、高速铁路大桥等方向开展基础和应用研究。
摘要
Super-long span bridges demand high design requirements and involve many difficulties when constructed, which is an important indicator to reflect the bridge technical level of a country. Over the past three decades, a large percentage of the new long-span bridges around the world were built in China, and thus, abundant technological innovations and experience have been accumulated during the design and construction. This paper aims to review and summarize the design and construction practices of the superstructure, the substructure, and the steel deck paving of the long-span bridges during the past decades as well as the current operation status of the existing long-span bridges in China. A future perspective was given on the developing trend of high-speed railway bridge, bridge over deep-sea, health monitoring and maintenance, intellectualization, standard system, and information technology, which is expected to guide the development direction for the construction of future super long-span bridges and promote China to become a strong bridge construction country.
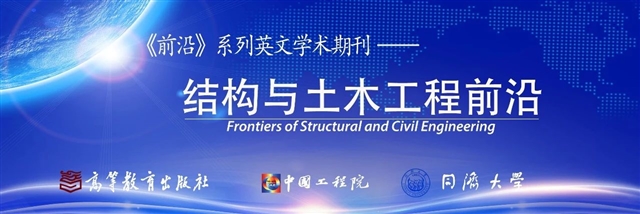
《前沿》系列英文学术期刊
由教育部主管、高等教育出版社主办的《前沿》(Frontiers)系列英文学术期刊,于2006年正式创刊,以网络版和印刷版向全球发行。系列期刊包括基础科学、
、工程技术和人文社会科学四个主题,是我国覆盖学科最广泛的英文学术期刊群,其中13种被SCI收录,其他也被A&HCI、Ei、MEDLINE或相应学科国际权威检索系统收录,具有一定的国际学术影响力。系列期刊采用在线优先出版方式,保证文章以最快速度发表。
高等教育出版社入选“中国科技期刊卓越行动计划”集群化项目。Frontier系列期刊中:13种被SCI收录;1种被A&HCI收录;6种被Ei收录;2种被MEDLINE收录;11种中国科技核心期刊;16种被CSCD收录。
中国学术前沿期刊网
http://journal.hep.com.cn
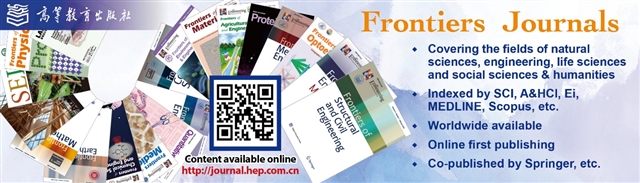
特别声明:本文转载仅仅是出于传播信息的需要,并不意味着代表本网站观点或证实其内容的真实性;如其他媒体、网站或个人从本网站转载使用,须保留本网站注明的“来源”,并自负版权等法律责任;作者如果不希望被转载或者联系转载稿费等事宜,请与我们接洽。