中国科学院大学2021年本科录取通知书曾被称为“最硬”通知书,皆因其中嵌着一块刻有校训“博学笃志、格物明德”的金刚石。
这批刻有校训的金刚石,由中国科学院宁波材料技术与工程研究所(以下简称宁波材料所)制作完成。
经过多年努力,该所成功打通了从理论探索到装备与工艺国产化,再到高品质大尺寸单晶高效制备和规模量产的全链条,成功研发出我国首条化学气相沉积(CVD)大单晶金刚石生产示范线,为我国在半导体技术领域实现弯道超车、抢占未来产业的制高点,以及实施国家发展战略提供了支撑。
江南回江南
2010年,作为美国应用纳米材料控股公司的科学家,东北汉子江南得知,成立不到7年的宁波材料所面向全球招聘研究人员。
江南深耕材料领域多年,一直牵挂祖国的发展。他深知,只有回国才有机会让所学的知识发挥出最大价值,于是很快与时任宁波材料所所长崔平取得联系。
两人科研理念一致,尤其让江南心动的是,宁波材料所非常重视成果落地及产业化,这与他在产业界多年形成的认知不谋而合。
不过江南希望在更合适的时机回来,宁波材料所愿意给人才更多的时间思考和成长。之后的两年,崔平一直与江南保持联系,交流学界、产业界新动态。
到2012年,江南已经手握中、日、美专利50余项,发表学术论文80余篇。经过梳理和沉淀,他希望在CVD单晶金刚石制备及相关生产设备上发力。“更合适”的时机到来了。
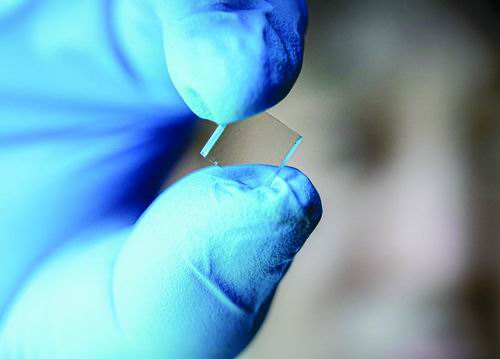
CVD单晶金刚石。
当时,国际上已经有个别机构能够使用CVD法生产金刚石,但售价很高。国内个别厂家虽然有生产装备,但由于腔体设计有缺陷、等离子体不稳定、气密性及合成工艺有问题,没有成功生产的先例。
回国前就有人建议江南使用国外设备,因为“国内设备长不出单晶金刚石”。
江南却颇有信心,他说:“不必迷信,国外有的机构也就一两位博士主持研发,而国内那么多科研力量,我们一定行!”这也是后来进入研发团队的许多人秉持的信念。
江南加入宁波材料所前的人才引进评审会由中国工程院院士、时任宁波材料所科学技术委员会主任薛群基主持。
薛群基介绍,当时国内用高温高压法生产金刚石的企业很多,出口量也很大,但缺乏高技术层面的应用。
“有专家对江南要做的CVD单晶金刚石研发不看好,毕竟那时连靠谱的国产设备都没有。”薛群基回忆说,“当时虽然宁波材料所很年轻,但作为国家战略科技力量的一员,应当围绕高技术应用、面向国家战略需求开展研究,这就需要有水平、有信念的人才。”
而江南正是这样的人才,因此他顺利成为宁波材料所的一员。
“种”钻石
金刚石听起来就很贵重,事实也是如此。它更为人熟知的名字是“钻石”,由于其切割、打磨后璀璨夺目,因此在饰品市场颇受追捧。
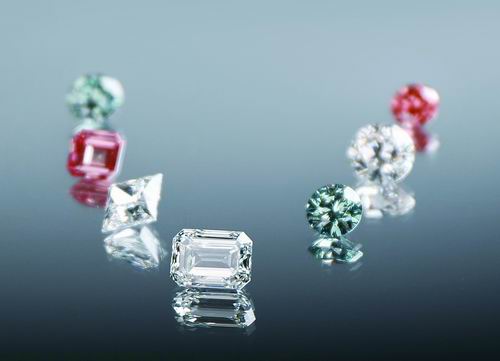
克拉级透明钻石和彩色钻石。
此外,金刚石是精密切削和精密加工的关键。“几乎所有高端制造业产品都依赖它。”江南介绍,从光学镜头到我国大科学装置的反射盘,都离不开金刚石刀具的超精密加工。
然而,天然金刚石十分稀有,很难在工业领域实现大规模应用。
20世纪50年代,美国通用公司开始采用高温高压法,模拟天然金刚石“老家”地幔层的温度与压力,制备金刚石。由于具有综合优势,目前依然有大量国内外企业使用这种方法制备金刚石。
但高温高压法生产出的金刚石颗粒形貌、大小和品质各异,难以应用于半导体及微电子等高技术领域,于是从20世纪60年代开始,美国学者就尝试用CVD法培育金刚石。
“培育过程有点像种庄稼,需要‘种子’与‘养料’。”江南介绍,开始培育时,需要一块小尺寸的金刚石作为籽晶,也就是“种子”,以甲烷等碳源气体作“养料”,在超真空培养舱中,将气体原料中的碳原子分离出来,让它们一层一层沉积在籽晶片上,逐渐长厚,最终籽晶就成长为更厚、更大的金刚石晶体了。
CVD人造金刚石与天然金刚石结构相同、化学成分相同,就连物理性质也相同,而且由于技术进步和生长环境更加洁净无瑕,反而比天然金刚石纯净度更高。
江南认为,天然金刚石是大自然的馈赠,而人造金刚石则是人类科技硬实力的展现。
造设备
2012年底回国的时候,江南只身一人,携带简单的个人用品,轻装出发。那时宁波材料所经费并不充裕,但仍为江南提供了当时最高的科研启动经费。
江南团队的第一位成员是科研兼行政助理戴丹,第二位成员是来自湖北的硕士毕业生吕继磊,专业方向是金刚石。
帮手有了,江南决定尽快启动科研工作。他们想用微波等离子CVD(MPCVD)法实现单晶金刚石的同质外延生长。原理是在微波能量的作用下,将原料气体激发成等离子体状态,直到实现辉光发电,腔体中充满过饱和原子氢和含碳基团,从而有效提高单晶金刚石的沉积速率和质量。为此,先要配备相关设备。
当时,国外已经实现CVD金刚石的生产,但进口一台设备要花近300万元,太贵了,而且只买一台也不能满足批量生产需求。江南决定在国产设备基础上进行研发,让国产化实现得更彻底。
吕继磊跟着江南到成都等地的几家设备厂商寻求定制。“江老师很有经验,也不多说废话,直接去设备现场,结果发现设备确实非常不成熟。比如腔体做得不均匀、材料本身不均匀,甚至有的地方用铁替代不锈钢,就连等离子体都是偏的……”对于10多年前的那段经历,已成为企业家的吕继磊记忆犹新。
这一轮定制之旅,用了很多天,白天测试、晚上总结。当他们将这些优化意见提交给厂家时,对方很吃惊。厂家每年只生产几台设备,没想到买家这么“麻烦”。不过,意见提得有理有据,厂家只能按要求进行修改。
就这样,2013年盛夏,一台相对靠谱的MPCVD设备终于造出来了。那天,来自宁波材料所的科研人员离开设备厂区后,驱车一个多小时到成都市中心的武侯祠喝茶,心情很好。
“种”成了
2013年8月初的一天,MPCVD设备到位了。放置籽晶开机后,这台设备几乎成了江南等人的全世界:凌晨两三点准备下班前,要看一下设备;早上8点多来实验室,第一件事是看设备;上班过程中,80%的时间都在看设备,观察金刚石生长情况、参数波动,随时记录,以应对突发情况。
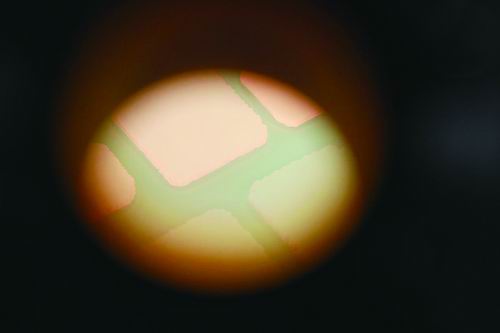
生长中的CVD金刚石。
然而,过了近一个月,金刚石还没“种”成功,设备却开始出现各种问题。
MPCVD设备的谐振腔关系着金刚石的生长效率,其设计、制造需要考虑尺寸、真空密封方式,承载晶片的基片台的性状、材质、散热方式,以及电源、水冷系统、气源系统等整个设备的外围稳定性。
由于厂家也不熟悉需要的工艺,江南只能带领团队亲自动手拆了改、改了装,3个多月内把这台设备“大卸八块”不止100次,有时候一天拆两次。“上百次的失败,每次都很沮丧,不是设备不稳定就是部件出问题,长出黑乎乎的已经不能称之为晶片的金刚石。”江南回忆说。
直到11月,崔平帮忙找到一家专门做腔体的企业,情况才有所好转。这家企业的负责人很专业且尽心尽责,双方结合各自经验逐步摸索,先通过模拟软件大量计算得到理论中的最优值,再通过经验叠加,得出实际的最优参数。
升级后的设备各方面得到优化——密封圈不再使用易老化、易熔化的橡胶圈,在试验过氟胶圈、聚氨酯圈等材料后,最终确定为金属密封圈;基片台材质从热导率差、易变形的不锈钢换成铜……随着工艺的改进,江南预判到了成功合成单晶金刚石的节点。
此后,团队又招进两名研究生,大家可以轮班看设备了。
2013年12月31日深夜,科研人员准备下班前再次到观察窗查看,得到了一份新年礼物——第一颗金刚石“种”成功了!这份特殊而贵重的礼物,让在场的每一位科研人员终生难忘。他们把这颗3毫米×3毫米×1.5毫米的人造金刚石放在石英石表盘上,拍下它的第一张照片。
作为国内第一片使用自主研发的CVD装备及工艺合成的单晶金刚石,它的诞生不仅意味着整个人造金刚石产业链条的生态可能发生改变,更意味着我国人造金刚石的高技术应用不再受制于人。
产业化
然而,差距依然存在,同一时间,国外已经“种”出5毫米×5毫米、7毫米×7毫米的CVD金刚石。更紧迫的是,尽管江南等人制造的MPCVD设备成本虽然不到30万元,只有进口机的1/10,但仅凭团队的经费,依然捉襟见肘,难以实现CVD单晶金刚石的规模化制备。
2013年,同为宁波材料所高级引进人才的激光专家张文武,介绍他的河南老乡张军安夫妇来和江南谈合作。
崔平对成果转化颇有经验,也一起参与了交流。她对当年的情形印象深刻:“这对夫妇非常朴实,貌不惊人,但是一聊就知道他们特别懂行。”
张军安在河南一直做高温高压金刚石生产,不过产出的都是粉体。对于江南实验室长出来的块体,他觉得,技术这么先进,未来市场一定没问题。
崔平很看好张军安夫妇的诚意和对产业链、市场的熟悉,认为可以和江南很好地互补。“科学家就做研究,设备购买、产品销售这些事交给企业家,这是最好的组合。”
合作就此达成。张军安投入上千万元,一半用于支持团队继续做科研,一半用来与江南、张文武共同创办宁波晶钻公司。
宁波材料所非常支持这种一边研发,一边产业化的发展方式,还专门开会研讨了推动创办企业的细节,助力企业更具市场活力。
快车道
2013年,宁波晶钻公司成立并实质性运营后,CVD单晶金刚石技术和国产化生产就此驶入快车道。
2014年3月,经过优化的第二台MPCVD设备制造完毕,它的等离子体更大,确保了更大、更稳定的有效沉积面积,从一次只能放1颗籽晶变成可以同时放9颗籽晶,生长时间则从一个星期缩短为3天。整体生产效率大幅提高。
在此基础上,经过又一轮优化,第三批10台设备“一气呵成”。2014年下半年,它们被整整齐齐地安放在宁波晶钻厂房并启动,标志着我国首条CVD大单晶金刚石生产示范线正式投产。
为了进一步实现CVD单晶金刚石生产工艺的国产化,这10台机器轮番试验各种不同的工艺,帮助科研人员做了大量摸索。
在不断优化、迭代中,MPCVD设备2016年达到20台、2017年达到30台,“种”出的金刚石尺寸提升到7毫米×7毫米、10毫米×10毫米……设备和工艺也都完全实现了国产化。
截至2023年底,全球约有1万台MPCVD设备,我国有3000台左右,其中宁波晶钻拥有1000余台,成为全球规模最大的CVD单晶金刚石生产商之一,实现全自动化机器人监控运转,产品尺寸最大达42毫米×42毫米,品质对标世界先进水平。
当初,需要花10万元从国外购买的单晶金刚石籽晶,目前,只需要几百元成本就能得到了。
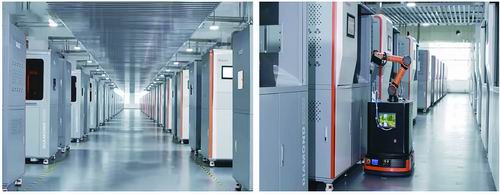
CVD单晶金刚石全自动化生长车间。宁波材料所供图
无人区
2016年从宁波材料所科技处岗位转入江南团队的研究员李赫,其实早就与江南开展了合作研究。
这一年,他依托江南团队申请到宁波市重大科研专项,决定全身心加入团队,并主动策划、申请包括国家重点研发计划在内的重要科研项目。
如今,这支团队已发展成为拥有包括4位国家级高层次人才在内的近百人的科研队伍,早已不复江南一人的冷清。
自10年前宁波建起国内首条自主研发的CVD单晶金刚石生产线起,国内已建立了2英寸级金刚石MPCVD装备国产化制造、金刚石衬底激光切割剥离技术与装备国产化制造、金刚石热化学研磨抛光技术与装备国产化制造等分支行业。培育钻石、金刚石工具等新兴产业终端市场规模超千亿元。
宁波材料所这群充满信念的科研人员,已经从原来的跟跑、并跑,真正进入了领跑的“无人区”——正如当初薛群基期待的,他们希望能建立起金刚石半导体产业高端新赛道,打造第四代金刚石半导体创新产业链,实现金刚石在芯片、微电子、量子通信、光学、超精密加工、高端医疗等领域的创新应用。
李赫坦言,现在心里是忐忑的。“以前知道别人做出来过,我们有信心做出来,心里是轻松的;并跑甚至有望超越的时候,是很有成就感的;现在国内外都没有参照物了,难度非常大,压力一定是有的,但我们寻求突破的动力依然很强。”
2023年,团队在中国科学院项目的支持下,率先开发出可实现12英寸超大尺度高品质金刚石制备的大功率MPCVD装备与合成工艺。该技术为金刚石晶圆的高效率、低成本产业化合成提供了重要途径。
目前,团队正紧锣密鼓地进一步全面优化装备与工艺。同时,相应大尺寸金刚石晶圆激光隐切技术和芯片级精度研抛技术也亟待开发。新赛道的建立,意味着团队的工作更多,江南又开始带领团队夜以继日地进行高强度攻关。
金刚石被誉为“终极半导体”材料。“目前在CVD金刚石技术方面,总体来说国内外处于并跑阶段,实现领跑,是时代赋予我们抢占新一代半导体科技制高点的一个重大机遇、重大挑战,同时也是国家在半导体领域实现超越的希望所在,因此不能错失良机。”江南说。
“我相信,未来几年,通过国内优势单位跨界协同、联合创新,完全能够率先打通金刚石晶圆制造的新赛道,撬动万亿级高端新市场,开创半导体研究新领域。”对此,江南充满信心。
版权声明:凡本网注明“来源:中国科学报、科学网、科学新闻杂志”的所有作品,网站转载,请在正文上方注明来源和作者,且不得对内容作实质性改动;微信公众号、头条号等新媒体平台,转载请联系授权。邮箱:shouquan@stimes.cn。