|
|
基于新复合材料的高灵敏度应变传感器印制 | MDPI Applied Sciences |
|
论文标题:Printability of the Screen-Printed Strain Sensor with Carbon Black/Silver Paste for Sensitive Wearable Electronics
期刊:Applied Sciences
作者:Xue Qi, Heebo Ha, Byungil Hwang and Sooman Lim
发表时间:6 October 2020
DOI:10.3390/app10196983
微信链接:
https://mp.weixin.qq.com/s?__biz=MzI1MzEzNjgxMQ==&mid=2649977433&idx=3&sn=
8496f2bc313fdd994e2eac21be8edb24&chksm=f1dec89dc6a9418bae9a34339c06851d
3eafbab23a8a211f6e0b2f29dc0fd771ec1b7d5c992f&token=940521072&lang=zh_CN#rd
期刊链接:https://www.mdpi.com/journal/applsci
在过去的几十年中,印刷电子产品引起了科学界和工业界的广泛关注。然而到目前为止,基于可印刷性对其感测性能的系统研究尚未见报道。
本文作者提出了一种简单、低成本的方法:利用炭和银纳米复合材料,通过丝网印刷工艺,来制造高柔性、高性能的敏感应变传感器。在制备过程中,系统地研究了浆料流变性能和印刷图案尺寸对传感性能的影响,以调整传感性能最优化。
实验部分
1.CB/Ag浆料制备
采用一种简单、低成本和低温的化学溶液工艺制备炭黑和银纳米颗粒的浆料。树脂、分散体和溶剂以4:1:8的质量比混合,炭黑固体含量占比分别为3.5%、17.5%和31.5%。原料用涡流搅拌器搅拌,每分钟1000转,搅拌3小时,将糊状物加入混合物中,搅拌20分钟,浸泡5分钟,重复三次。
2.CB/Ag应变传感器的研制
首先将不同配比的配方浆料加载到筛网上,以10cm/s的速度和6.8 mm的压力挤压0.3 mm,如图1a所示。然后,将打印的图案放在120摄氏度的真空烘箱干燥1小时。将打印的传感器连接到镍带和银涂层,以评估其性能。
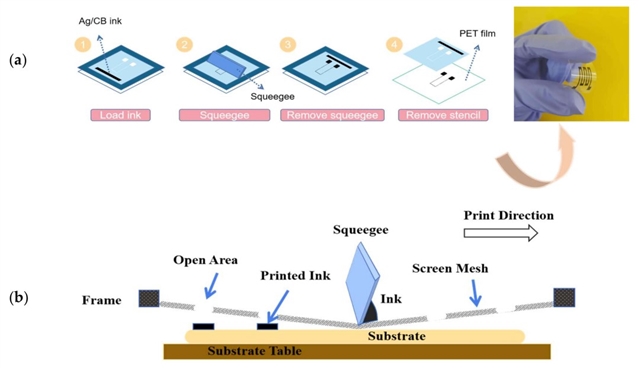
图1. (a) 印刷工艺原理图与 (b) 整体工作原理配合CB/AgNPs可穿戴式应变传感器。
结果与讨论
图1b显示了在PET基板上制造基于CB/AgNP的应变传感器的丝网印刷工艺。在CB/AgNP浆料由于挤压压力而通过开口网孔渗透到基材中后,筛网通过拉力从基材上折断,形成特定图案的浆料。图2显示了使用锥板流变仪确定CB固体含量对图案质量的影响时CB/AgNP浆料的流变行为。CB/AgNP-L,CB/AgNP-M和CB/AgNP-H的CB/AgNP比率分别为9:1、5:5和1:9。根据图2a所示的稳态流动测试,在不同剪切速率下测得的粘度表明,所有三种浆料均表现出剪切稀化行为。对于CB/AgNP-L,CB/AgNP-M和CB/C,剪切速率从1.4到0.4 Pa.s,130.4到1.0 Pa.s和486.0到0.4 Pa.s时,浆状油墨的粘度降低。这表明所有配制的油墨都适用于丝网印刷工艺。随后,在参考区间 (0–30s)、高剪切区间 (30–60s) 和再生区间 (60–150s) 进行峰持步 (PHS) 试验,如图2b所示。该工艺模拟了实际的丝网印刷工艺,其应力值随时间间隔的变化而变化,说明了浆料流动具有粘弹性特征。另外,三种用于确定模式4的10保真度浆料的回收率与CB浓度成正比;回收率依次为CB/AgNP-H (3.5%)、CB/AgNP-M (17.5%)、CB/AgNP-L (31.5%)。这些值见于表1中。图2c表明,从恢复行为看,PHS测试结果与模式保真度有显著相关。随着回收率按CB/AgNP-L、CB/AgNP-M的顺序增加,图案的尺寸更接近所期望的尺寸,线边锐度增加。
在这种情况下,由于印刷后恢复时间过短,不适合浆料的充分流平,导致在蒸发过程中出现空斑。此外,由于粘度过高,膏体更有可能陷入网孔。因此,选择CB/AgNP-M作为优化浆料。

图2. (a) 稳流试验和 (b) 峰持步 (PHS)试验,研究不同配比CB/AgNPs浆料的流变行为。(c) 不同CB浓度印刷图案的显微镜图像。PHS- peak hold step; CB- carbon black。
表1. 不同的印刷工艺步骤和不同剪切速率下的Ag/CB油墨粘度。

如图3a所示,作者制作了6个具有不同线宽 (100微米和300微米) 和长度 (25、52毫米和78毫米)、厚度为110微米的应变传感器,以研究图形尺寸对灵敏度的影响。由于电阻式传感器是由电极组成的,其电气性能对获得高灵敏度至关重要。图3b给出了1–5 v梯度电压下样品的I-V曲线,其中电流输出随着外加电压的增加而变化。根据每条线的线性斜率,六个不同的应变传感器表现出均匀的电导率。此外,宽度越大、长度越短的传感器电流越大,根据欧姆定律,这是合理的。

图3. (a) 不同长度和宽度的丝网印刷传感器图片;(b) 丝网印刷的CB/AgNPs在各种尺寸下通过线的测量电阻。
使用印刷传感器的优点是其灵敏度可控。图4a显示的GF根据所施加的应变对传感器进行测量。GF计算公式如下:
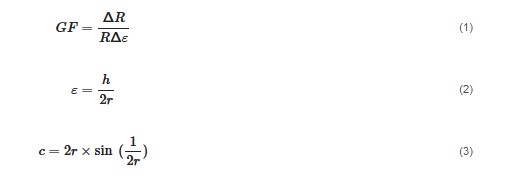
随着应变的增加,应变相关的响应单调地增加。当应变对传感器施加在0.61%–1.44%范围时,决定传感器灵敏度的GF为192.77–444.6,据我们所知,这是目前报道的基于CB的大应变印刷传感器中最高的规格因子。此外,还可以通过尺寸效应来控制灵敏度。表2显示了CB/AgNP浆料在灵敏度方面与之前的文献结果相比的优异性能。CB/AgNP浆料在拉伸压力下结阻变化较大,因此可以产生较高的GF,如图4b所示。导电膜中的电子可以穿过重叠的纳米材料的渗透晶格,传感器的弯曲会导致重叠区域的减少甚至失去电连接,从而增加电阻。

图4. (a) 丝网印刷的CB/AgNP线在不同的长度和线宽下,传感器在各种应变下的动态弯曲-释放周期响应为0.61–1.44%。(b) CB/AgNP浆料的感应机理示意图以及丝网印刷的CB/AgNP浆料的表面SEM图像。
表2. 比较了以往报道的基于炭黑的应变传感器的规格因子 (GF)。

作者研究了该传感器的机械灵敏度和耐久性,以评价该传感器在可穿戴电子设备中的应用性能。从图5a可以看出,在不同的应变值下,响应连续而均匀的增加,可以看出计算的线性度为R2 = 0.9974。图5b显示了印刷CB/AgNP传感器的高耐久性,在施加的应变为0.275%的情况下,超过1000次的反复弯曲-释放循环。以上所有的响应都是在无噪声的情况下得到的。具体反应如图5所示。在实际操作中,附着在人体上的传感器会受到各种环境条件的影响。因此,其在不同的温度和湿度条件下,需要有较高的稳定性。图5c显示,随着温度从20摄氏度升高到120摄氏度,阻力变化了1.3%。另外,湿度为70%时的电阻变化为0.057%,如图5d所示。这一结果主要是由于炭黑及其钝化层的内在性质所致。然而,在湿度超过70%时,观察到的性能不稳定,这可能是由于水通过被动式层的可能性很高。

图5. (a) 不同应变连续渐进输入。(b) 复合材料1000次循环、低拉伸变形的耐久性。(R/R0为多次弯曲释放周期的函数CB/Ag复合材料的应变为0.275%。?R为弯曲和时的电阻差释放时,R是松弛状态下的初始阻力。温度 (c) 和湿度 (d) 对CB/Ag (CB-h)应变传感器电导率的影响。
由于CB/AgNP应变传感器具有高度的灵活性、可扩展性和灵敏度,可以应用于穿戴式柔性人体运动检测平台。图6a显示的响应传感器附在一个手指在弯曲角度的0–90°。此外,将CB/AgNP应变传感器安装在人体颈部,用于检测头部旋转。具有较高的灵敏度,可以准确反映头部旋转情况,如图6b所示。
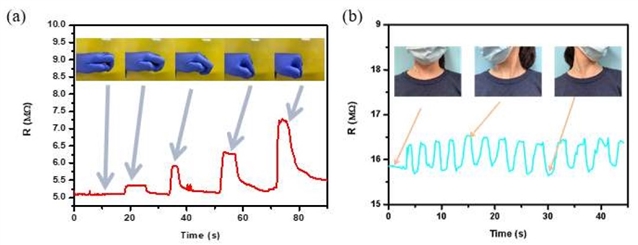
图6. 基于CB/AgNP纳米复合应变传感器的人体运动检测。(a) CB/AgNP应变传感器对0–90°弯曲角度的响应。(b) 头部左右转向的运动检测。
综上所述,本文亮点在于提出了一种基于CB/AgNP复合材料的新型丝网印刷应变传感器。并且研究了不同宽度和长度的印刷传感器的电学性能,评估了应变传感器的灵敏度。作者表示,这是目前所报道的印刷传感器中在该应变范围内最高的灵敏度。而且,该传感器在恶劣环境下能稳定地显示出电阻变化。
Applied Sciences (ISSN 2076-3417,IF 2.474) 作为开放获取型国际期刊,主要发表应用自然科学研究领域相关的论文。期刊包括光学和激光、纳米技术和应用纳米科学、能源、材料、化学、机械工程、应用生物科学和生物工程、环境和可持续发展的科学技术和计算与人工智能等24个部门。Applied Sciences采取单盲同行评审,一审平均周期约为15.9天,文章从投稿到发表平均仅需35天。
摘要:
Printing technology enables not only high-volume, multipurpose, low-impact, low-cost manufacturing, but also the introduction of flexible electronic devices, such as displays, actuators, and sensors, to a wide range of consumer markets. Consequently, in the past few decades, printed electronic products have attracted considerable interest. Although flexible printed electronic products are attracting increasing attention from the scientific and industrial communities, a systematic study on their sensing performance based on printability has not been reported so far. In this study, carbon black/Ag nanocomposites were utilized as pastes for a flexible wearable strain sensor. The effects of the rheological property of the pastes and the pattern dimensions of the printed electrodes on the sensor’s performance were investigated. Consequently, the printed sensor demonstrated a high gauge factor of 444.5 for an applied strain of 0.6% to 1.4% with a durability of 1000 cycles and a linearity of R2 = 0.9974. The sensor was also stable under tough environmental conditions.
Experiments
Chemicals
CB was purchased from the graphene market (South Korea). AgNPs were purchased from NTbase (South Korea), and the model of AgNPs was NP-S80 with a purity of 99.99%. A dispersion (BYK-180) was obtained from BYK (South Korea). 2-(2-Butoxyethoxy) ethyl acetate (99.0%) and 2-ethoxyethyl acetate (99.0%) were supplied by Samchun Pure Chemical Co., Ltd. (Pyeongtaek –si, South Korea). A PET film and silver paint (SPI-Chem) were also used as components of the sensor.
Paste Formulation of CB/Ag Paste
An easy, low-cost, and low-temperature chemical solution process was used to prepare the CB/Ag paste. The resin, dispersion, and solvent were mixed in the weight ratio of 4:1:8 with the CB solid contents of 3.5, 17.5, and 31.5 wt%. The materials were mixed using a vortex agitator (Daihan Scientific) at 1000 RPM for 3 h. The paste was added to the mixture for 20 min, the mixture was soaked for 5 min, and this process was repeated three times.
Fabrication of CB/Ag Strain Sensor
The formulated pastes with different ratios of materials were first loaded onto screen meshes (mesh count 400, Samborn Screen, South Korea) and squeezed with a snap-off distance of 0.3 mm at a speed of 10 cm/s and a pressure of 6.8 mm, as shown in Figure 1a. Then, the printed patterns were dried in a vacuum oven at 120 °C for 1 h. The printed sensors were connected to a nickel tape and silver paint to evaluate their performance.
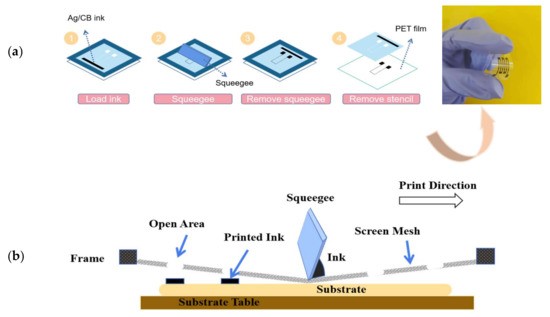
Figure 1. (a) The schematic diagram of printing process and (b) overall working principle with CB/AgNPs for wearable strain sensor.
Characterization
A mixed flow instrument (Discovery HR-3, New Castle, USA) was used to measure the viscosity of the Ag/CB ink. A current signal system (SourceMeter, Keithley 2400, Beaverton, USA) of voltage 5 V was used to test the durability of the sensor with a bending system (OWiS PS 10-32, Staufen, Germany). Optical microscope photographs were obtained using an electron optical microscope (Eclipse LV100ND/LV100NDA, Seoul, Korea). Scanning electron microscope (SEM) images were obtained with a field-emission scanning electron microscope (Carl Zeiss Supra 40VP, Oberkochen, Germany).
Results
3. Results and Discussion
Figure 1b shows the screen-printing process for the fabrication of the CB/AgNP-based strain sensor on the PET substrate. After the CB/AgNP paste penetrated the substrate through the opening mesh owing to the pressure of the squeeze, the screen mesh was snapped off the substrate by the tension, resulting in the specific pattern of the paste. The rheological property of the CB/AgNP paste and the related pattern fidelity should be considered to obtain the desired sensor. Figure 2 shows the rheological behavior of the CB/AgNP paste using a cone-plate rheometer to determine the effect of the solid content of CB on the pattern quality. The ratios of CB/AgNP were 9:1, 5:5, and 1:9 for CB/AgNP-L, CB/AgNP-M, and CB/AgNP-H, respectively. The measured viscosities at different shear rates from the steady-state flow test shown in Figure 2a reveal that all the three pastes exhibit shear-thinning behavior. The viscosity of the paste ink decreased as the shear rate increased from 1.4 to 0.4 Pa.s, 130.4 to 1.0 Pa.s, and 486.0 to 0.4 Pa.s for CB/AgNP-L, CB/AgNP-M, and CB/AgNP-H, respectively. This indicates the suitability of all the formulated inks for the screen-printing process. In addition, the CB/AgNP paste ink with a higher solid content of CB exhibited a higher viscosity at zero shear viscosity and above the shear rate, which indicates that the concentration of CB affects processability during the screen-printing process. Subsequently, a peak hold step (PHS) test involving holding the sample at different shear rates at three intervals, namely, the reference interval (0–30 s), high-shear interval (30–60 s), and regeneration interval (60–150 s), was conducted as shown in Figure 2b. This process mimics the actual screen-printing process, and the applied stress value varies according to each time interval, which elucidates the paste flow with a viscoelastic feature. The results show the general flow behavior of thixotropy, where a structural transition occurs due to mechanical pressure (through squeezing in this process). In addition, the recovery value of the three pastes to determine the pattern fidelity was proportional to the CB concentration; the recovery values were in the order of CB/AgNP-H (3.5%), CB/AgNP-M (17.5%), and CB/AgNP-L (31.5%). These values are listed in Table 1. Figure 2c indicates that the result of the PHS test was significantly related to the pattern fidelity according to the recovery behavior. As the recovery value increased in the order of CB/AgNP-L, CB/AgNP-M, and CB/AgNP-H at the same time interval, the dimensions of the pattern were closer to the desired dimensions, and the line edge sharpness increased. However, the recovery time (leveling time) is also an important factor in printability, as the abrupt recovery of CB/AgNP-H did not yield the best quality, as shown in Figure 2c. In this case, the excessively short recovery time after printing was not suitable for the full leveling of the paste, resulting in an empty spot during evaporation. Moreover, trapping of the paste into the mesh becomes likelier due to the excessively high viscosity. Thus, CB/AgNP-M was chosen as the optimized paste.
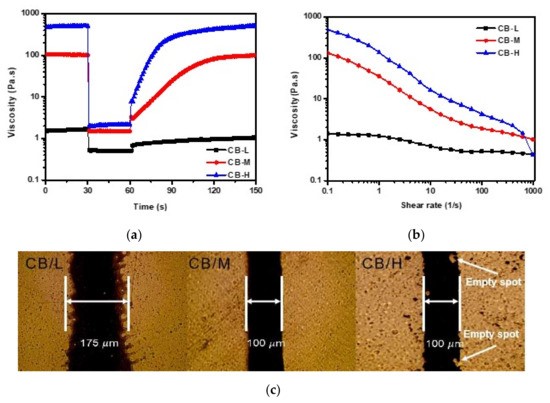
Figure 2. (a) Steady flow test and (b) PHS test to investigate the rheological behavior of CB/AgNPs paste with different ratios. (c) Microscope images of the printed pattern with different CB concentrations. PHS—peak hold step; CB—carbon black.
Table 1. Ag/CB ink viscosity at different shear rates, corresponding to different printing process steps.

Six strain sensors with various line widths (100 and 300 μm) and lengths (25, 52, and 78 mm) at a fixed thickness of 110 μm were fabricated, as shown in Figure 3a, to investigate the effect of pattern dimensions on the sensitivity. As the resistive-type sensor consists of electrodes, the electrical performance is important to attain a high sensitivity. Figure 3b reveals the I–V curves of the samples at a gradient voltage from 1 to 5 V, where the current output changes in accordance with the increase in the applied voltage. Based on the linear slope of each line, the six different strain sensors showed a uniform conductivity. In addition, the sensor having a larger width and shorter length tended to show a higher current, which is reasonable based on Ohm’s law.
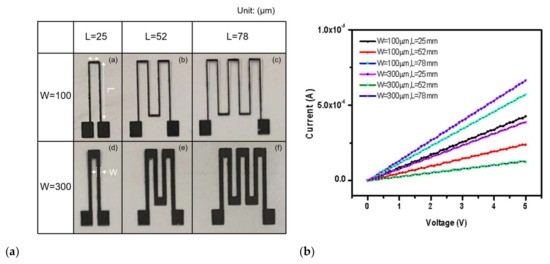
Figure 3. (a) Images of the screen-printed sensors with different length and width. (b) Measured resistance of the screen-printed CB/AgNPs past lines at various dimensions.
An advantage of using a printed sensor is its controllable sensitivity. Figure 4a shows the GF of the sensors according to the applied strain. The GF was calculated as follows:

where R refers to the initial resistance of the sensor under tension-free conditions; ε indicates the tensile strain when a stress is applied to the sensor; and ΔR indicates the resistance change. The thickness of the sensor, h, and the radius of curvature, R, in the bending process are affected by the applied pressure, whereas the radius of curvature can be calculated through the arc length, l, and chord length, c, in the bending process.
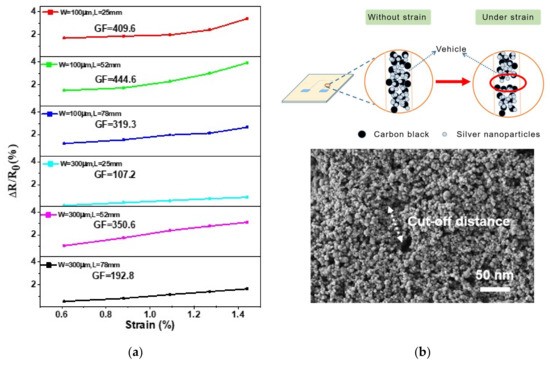
Figure 4. (a) Dynamic bending–release cycle response of the sensors for various strains 0.61–1.44% with the screen-printed CB/AgNP lines at different lengths and various line widths. (b) Schematic diagram of sensing mechanism for CB/AgNP paste and SEM image of surface for the screen-printed CB/AgNP paste.
It is observed that the strain-dependent responses increase monotonously with the increasing strain. With the application of strain in the range of 0.61% to 1.44% to the sensor, the GF determining the sensor sensitivity varied from 192.77 to 444.6, which is the highest GF among the CB-based printed sensors under a large strain reported so far, to the best of our knowledge. In addition, the sensitivity could be controlled by the dimension effect. Table 2 presents the excellent performance of the CB/AgNP pastes in terms of sensitivity in comparison with the previous results in the literature. The CB/AgNP paste could generate a high GF because the variation of junction resistance was severe under tension pressure, as shown in Figure 4b. The electrons in the conductive film can pass through a percolating lattice of overlapping nanomaterials, and the bending of the sensor can lead to a reduction in the overlapping areas or even a loss of electrical connections, increasing the resistance.
Table 2. Comparison of gauge factor (GF) of previous reported strain sensors based on carbon black.
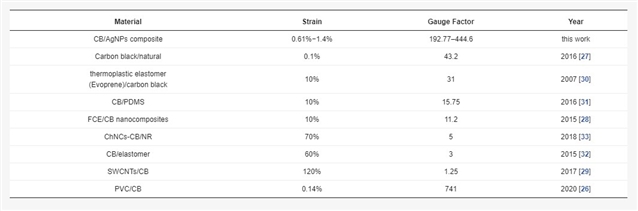
The mechanical sensitivity and durability of the sensor were investigated to evaluate the properties of the sensor for application in wearable electronics. Figure 5a shows the continuous and uniform increase in the response according to the applied strain with different values, which reveals the calculated linearity as R2 = 0.9974. Figure 5b displays the high durability of the printed CB/AgNP sensor over 1000 repetitive bending–releasing cycles at the applied strain of 0.275%. All the responses were obtained without any noise during the bending cycles. The specific response is shown as an inset. In practice, sensors attached to a human body are subjected to various environmental conditions. Thus, a high stability is required under various conditions of temperature and humidity. Figure 5c shows a resistance change of 1.3% with the increase in temperature from 20 to 120 °C. In addition, a resistance change of 0.057% for the humidity of 70% is shown in Figure 5d. These results are mainly attributed to the intrinsic property of CB and its passivation layer.However, an unstable performance was observed above the humidity of 70%, which may be attributed to the high possibility of water penetration through the passive layer.
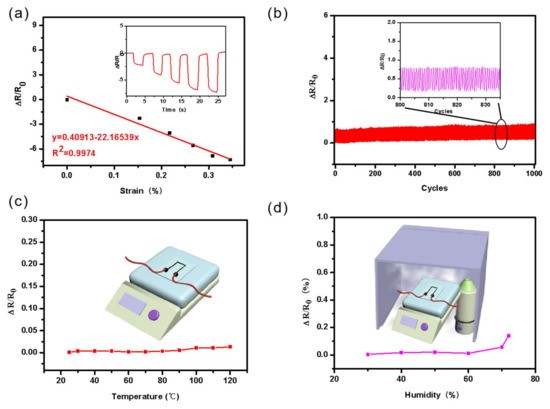
Figure 5. (a) Continuous progressive input of different strain. (b) Durability of composites under 1000 cycles with low tensile deformation. ΔR/R0 as a function of multiple bending and releasing cycles with 0.275% strain for CB/Ag composites. ΔR refers to the resistance differences under bending and release, R is the initial resistance in the relaxed state. Effect of temperature (c) and humidity (d) on the conductivity of the CB/Ag (CB-H) strain sensor.
As our CB/AgNP strain sensors are highly flexible, scalable, and sensitive, they can be employed in wearable and flexible human motion detection platforms.Figure 6a shows the response of the sensor attached to a finger at a bending angle of 0°–90°. In addition, the CB/AgNP strain sensor was attached to a human neck to detect head rotation. It demonstrated a high sensitivity to reflect head rotation accurately, as shown in Figure 6b.
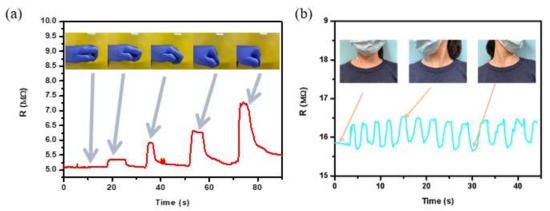
Figure 6. Human motion detection by the CB/AgNP nanocomposite strain sensors. (a) Response of the CB/AgNP strain sensor to the bending angles from 0° to 90°. (b) Motion detection of head turning left to right.
Conclusions
We proposed a new type of strain sensor based on CB/AgNP composites using a screen-printing process. The rheological property of the pastes was investigated to determine the pattern fidelity in accordance with the ratio of CB and AgNPs. The electrical performances of the printed sensors with different widths and lengths were investigated, to evaluate the sensitivity of the strain sensors. Consequently, a GF of 444.6 was obtained for the printed sample with the line width of 100 µm and the length of 52 mm at the applied strain ranging from 0.6% to 1.4%. This is the highest sensitivity at this applied strain range among the printed sensors reported so far, to the best of our knowledge. The sample also showed a high sensing linearity of R2 = 0.9974 and a high bending stability of 1000 cycles. In particular, the sensor revealed a stable resistance change under tough environmental conditions, demonstrating its feasibility for wearable applications.

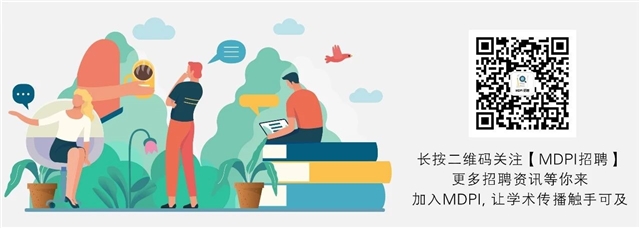
(来源:科学网)
特别声明:本文转载仅仅是出于传播信息的需要,并不意味着代表本网站观点或证实其内容的真实性;如其他媒体、网站或个人从本网站转载使用,须保留本网站注明的“来源”,并自负版权等法律责任;作者如果不希望被转载或者联系转载稿费等事宜,请与我们接洽。